TDKのコアテクノロジー
Vol.15
“SESUB”モジュールと「部品内蔵回路技術」
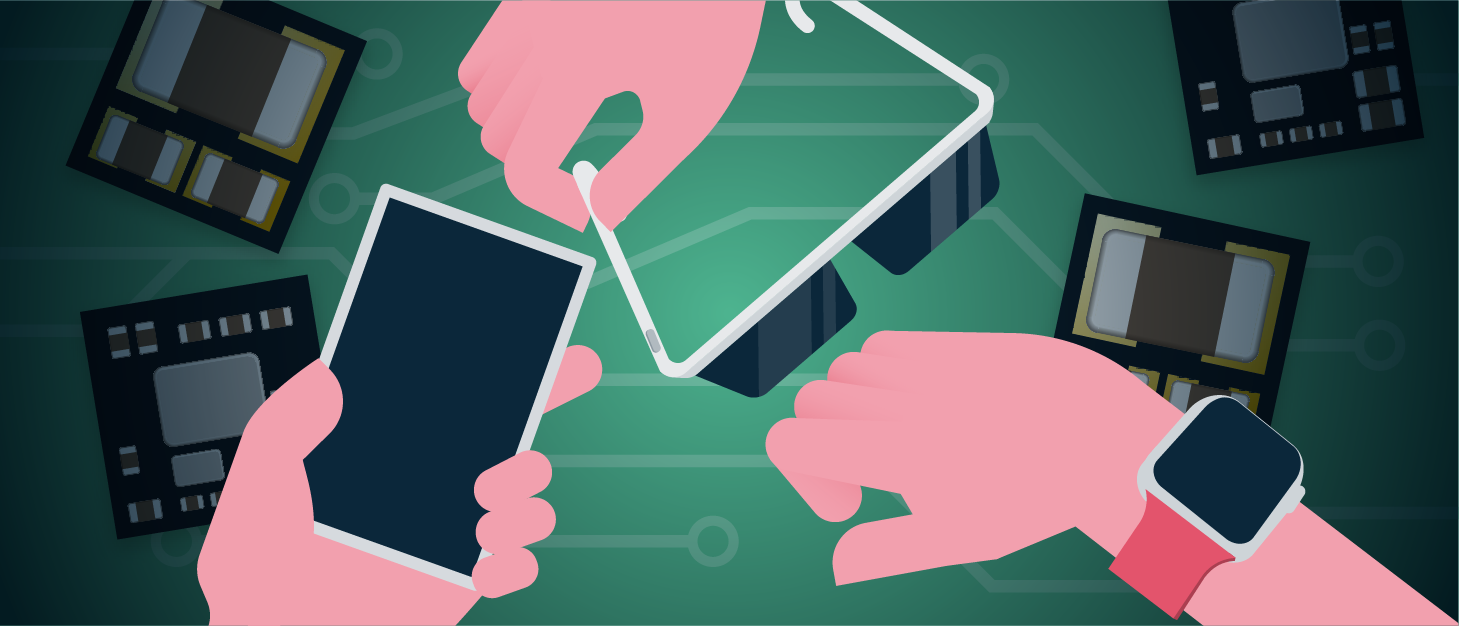
電子機器の高機能化とともに、プリント基板に実装される電子部品や配線パターンの高密度化が急速に進み、従来工法のままでは小型化の限界に近づきつつあります。そこで、この問題をブレイクスルーする方法のひとつとして注目されているのが、ICチップなどの電子部品を多層基板の中に埋め込む「部品内蔵回路技術」です。TDKは独自の製品設計技術を通じて、スマートフォンの電源管理モジュール、ウェアラブルデバイスやIoTデバイス用の通信モジュールなど、さまざまな分野で応用を拡大しています。
エレクトロニクス時代をもたらしたイノベーション
エレクトロニクス製品は、約10年単位でさまざまなイノベーションをもたらし、ライフスタイルを大きく変化させてきました。初のコンピュータといわれるENIAC(1946年)は、真空管1万7000本を使用した巨大な装置でしたが、そのデータ処理能力は現在では小さなICに収まってしまい、その機能はノートパソコンやスマートフォンの足元にも及びません。
真空管にかわるトランジスタやIC/LSIの発明やデジタル化を経て、現在もなおとどまることを知らないエレクトロニクスの技術進歩と開発トレンドは、「小型化・高速化・高機能化」です。
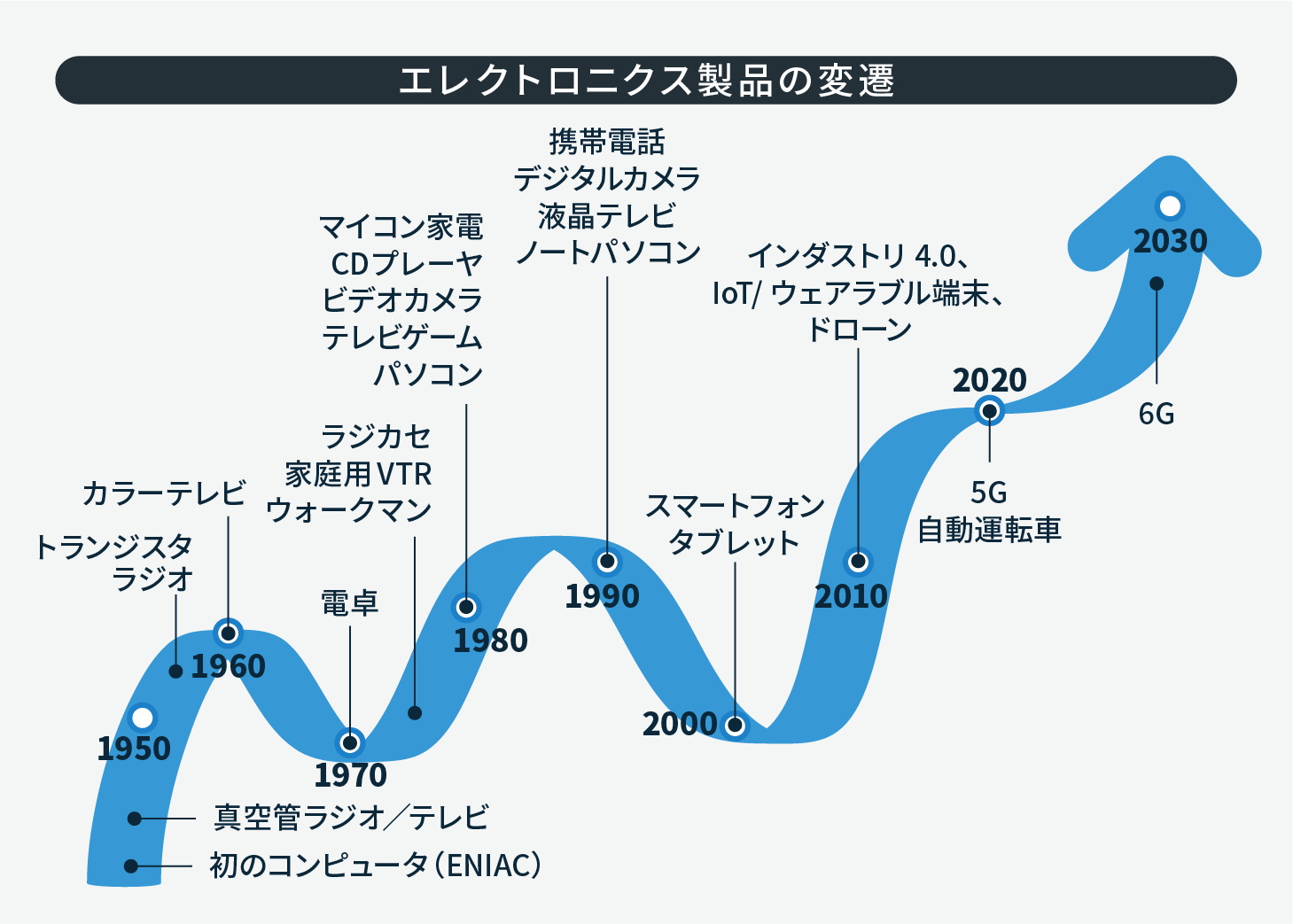
部品技術、実装技術、配線板技術の変遷
IC/LSIなどの半導体デバイスとともに、積層セラミックチップコンデンサ(MLCC)などのSMD(表面実装部品)も、回路基板の省スペース化と機器の小型化に貢献してきました。また、これらの電子部品をプリント基板に搭載する実装技術も進歩を遂げました。とりわけ、1980年代のエレクトロニクス製品の「軽薄短小」に大きく寄与したのは、日本の実装技術です。このため、“JISSO”は国際語として世界で広く使われるようになりました。
さらに、実装技術の進歩とともにプリント基板などと呼ばれる配線板技術も大きく変化し、片面・両面基板から多層基板、ビルドアップ基板、そして部品内蔵基板へと高度化しました。
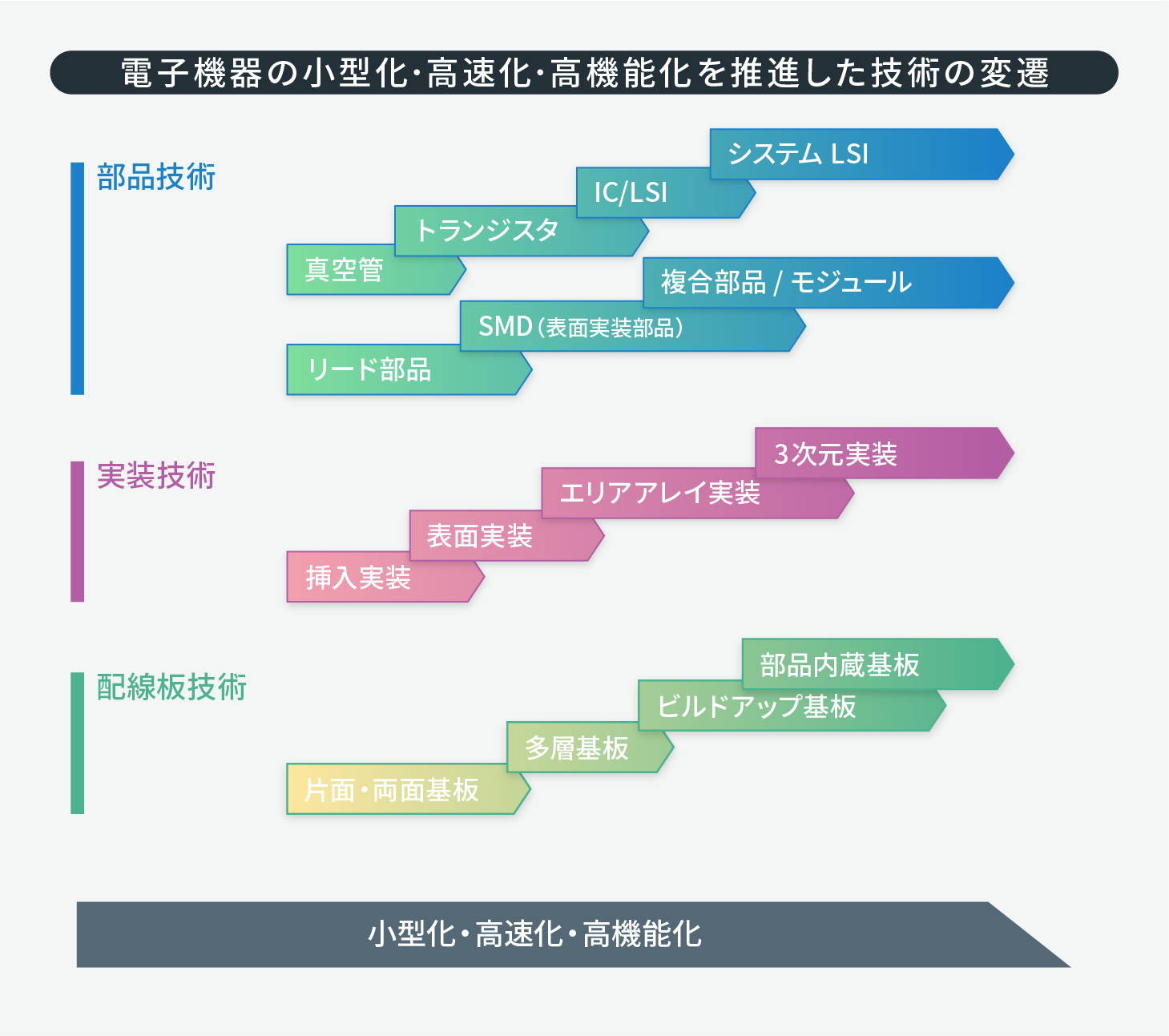
エリアアレイ実装から3次元実装技術へ
実装という用語は、一般にはプリント基板にコンデンサやインダクタ、半導体デバイスなどの部品をマウント(mount)あるいは挿入(insert)して搭載するという意味で使われますが、半導体デバイスの分野では、シリコンチップをプリント基板に接続するためのパッケージング(packaging)技術の意味でも使われます。
半導体プロセス技術の目覚ましい進展により、IC/LSIの集積度は同じチップサイズで当初の数十億倍にも及んでいます。しかし、リードフレームを用いた従来のIC/LSI製品は、チップサイズに比べてかなり大きくなってしまうのが難点です。このため、パッケージング技術の工夫により小型化が図られ、ICチップをはんだボールなどで基板に接続するBGA(ボールグリッドアレイ)などのエリアアレイ実装へ、さらには複数のICチップあるいはICパッケージをスタックする(積み重ねる)3次元実装技術へと進化してきました。
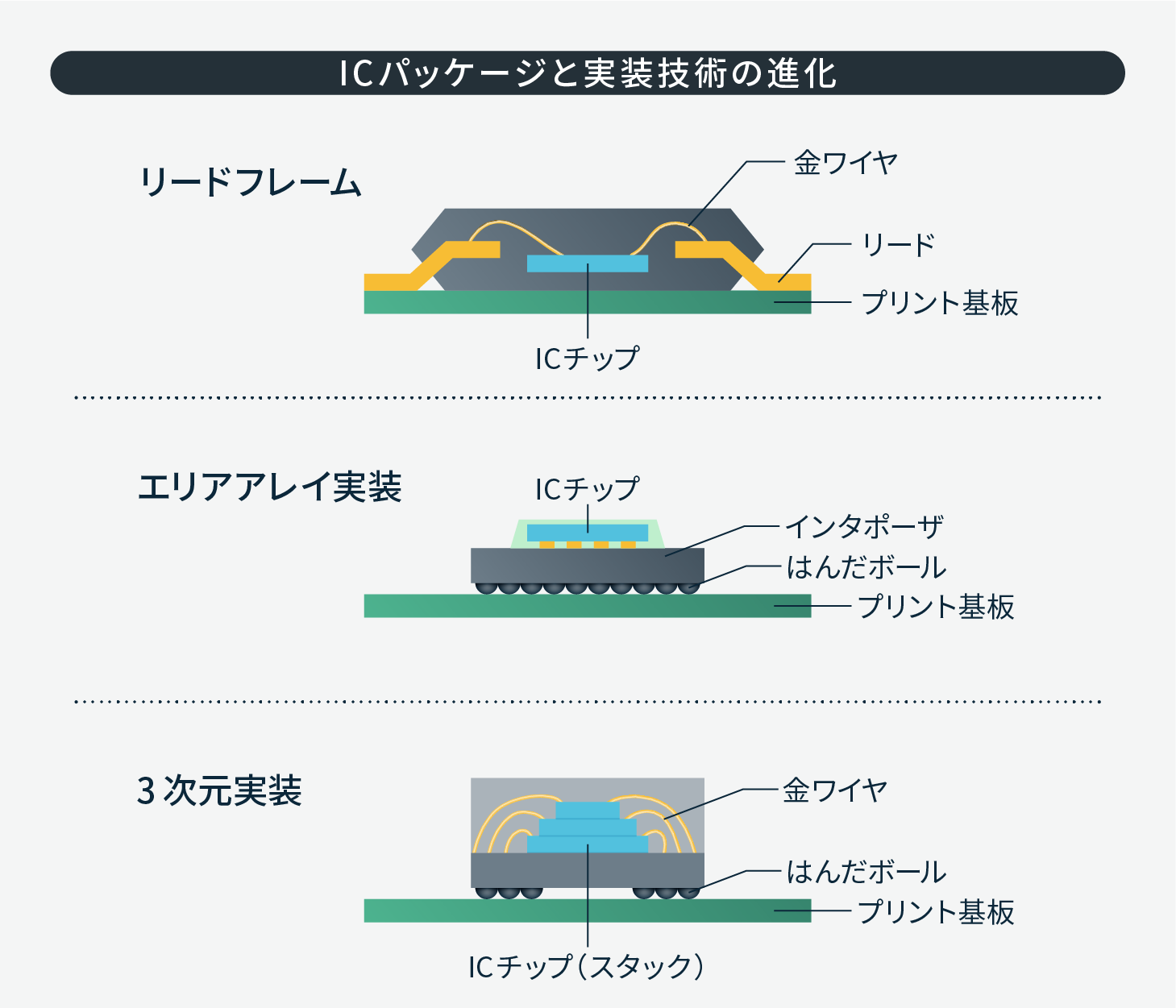
パッケージングされたIC製品をスタックする技術は、PoP(Package on Package)という。既存製品をそのまま利用できるがメリット。
「部品内蔵回路技術」が注目される理由
回路の高密度化への対策は、都市の過密化対策と似ています。3次元実装というのは、いわばビルの高層化に相当します。しかし、3次元実装でも高密度化の解消には限界があります。そこで発案されたのが、ICチップや受動部品(コンデンサなど)をプリント基板(PCB)に埋め込む、部品内蔵回路技術(Device Embedded PCB Technology)です。例えて言えば、過密化した都市の地下空間の有効活用です。ここにおいて、従来、地味な存在であったプリント基板が、一躍脚光を浴びることになりました。
プリント基板には、さまざまなタイプがありますが、従来の片面・両面基板にかわって、電子機器で多用されるようになったのは多層基板です。いずれも誘電体基材層のコア(ガラス繊維布+エポキシ樹脂など)に銅箔を貼ったもので、銅箔をエッチングすることで複雑な配線パターンが形成されます。多層基板は下図のように、コア基板(両面基板)の両面にプリプレグと呼ばれる接着性のある絶縁材シートと銅箔を貼り合わせて重ねたもので、銅箔の数が層数となります。
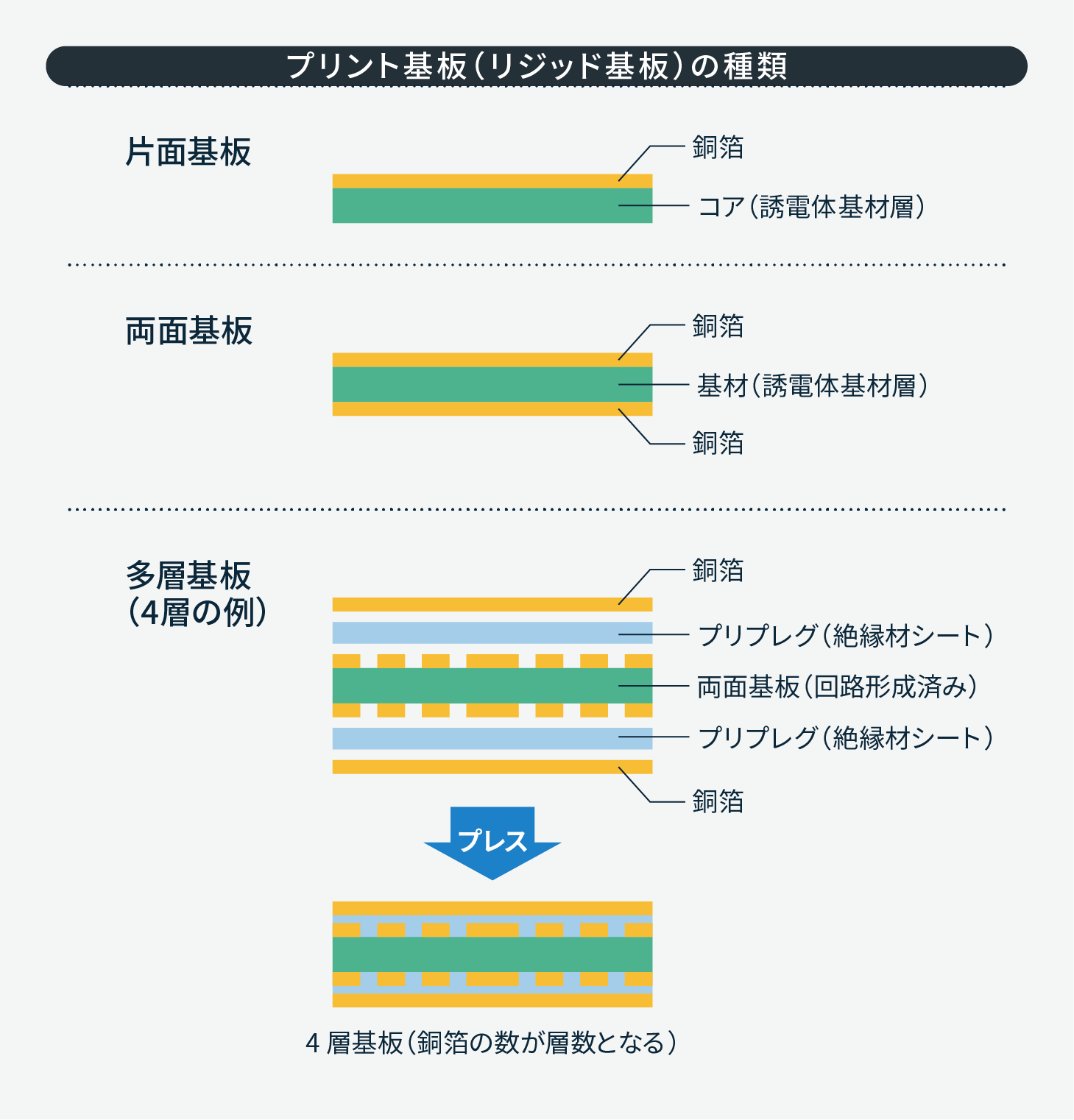
硬質の基材(絶縁樹脂)を用いたものをリジッド基板という。一部には柔軟な絶縁性フィルムに銅箔を貼ったフレキシブル基板も使われる。
多層基板とビルドアップ基板の違い
回路の高密度化にともなって配線パターンの占める面積が多くなると、多層基板でも対応が困難になります。また、配線パターンが長くなると、抵抗成分(ESR:等価直列抵抗)や寄生インダクタンス(ESL:等価直列インダクタンス)が大きくなり、信号品質を低下させたり、ノイズ発生の原因になったりします。
そこで、多層基板内部で高密度な立体配線をすることにより、省スペース化を図る配線板技術が開発されました。これがビルドアップ基板です。多層基板やビルドアップ基板には、下図のようにスルーホールやビア(ビアホール)と呼ばれる穴が設けられます。スルーホールは主にリード線部品を挿入するための貫通穴で、ビアは基板の層間を電気的に接続するためのものです。
ビルドアップ基板は、一層ごとにビア(ブラインドビアやべリードビア)をあけながら基板を積み重ねていく工法で、工数は多くなりますが、通常の多層基板よりも高密度な配線が可能になり、スマートフォンなどの回路基板として多用されています。
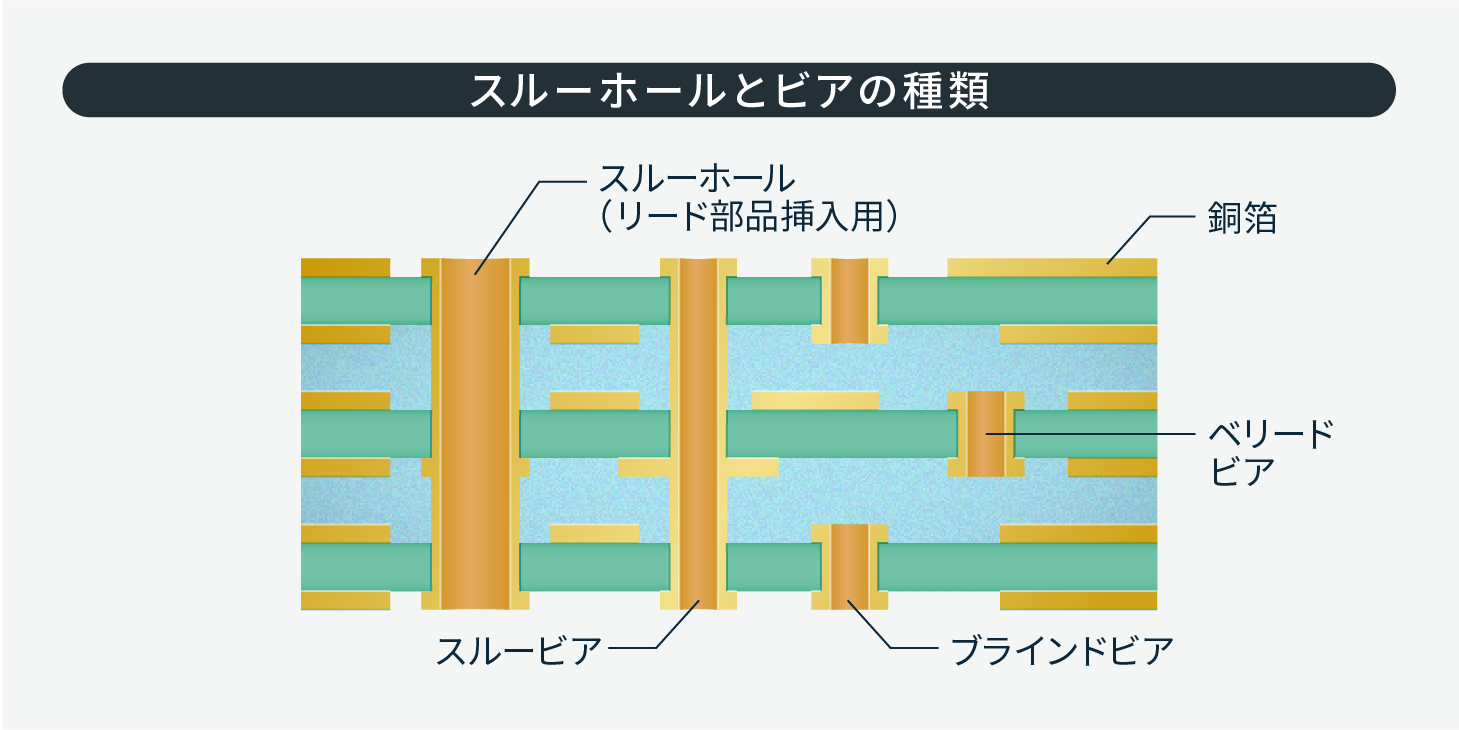
スルーホールやビアはドリルやレーザ光で穴あけ加工され、内部は銅めっきされる。
TDK独自のIC内蔵基板技術“SESUB(セサブ)”
TDKのIC内蔵基板技術SESUB(セサブ:Semiconductor Embedded in SUBstrate)は、ビルドアップ工法を用いた部品内蔵回路技術の一種です。すでに各種のSESUBモジュールとして実用化され、スマートフォンをはじめとするモバイル機器、IoT機器、ウェアラブル機器の小型化・高速化・高機能化に貢献しています。
3mm角サイズの超小型DC-DCコンバータ「μPOL」を例に、SESUBモジュールの製造プロセスの概要を以下に示します。
70~80µmに薄く加工し、個片化(ダイシング)したICをSESUB基板内部に埋め込み、ビア加工しながらビルドアップしてから、インダクタやコンデンサなどの外付け部品を搭載して製造されます。外付け部品を内部に埋め込むことも技術的に可能ですが、基板上に搭載することで、用途に応じた最適部品の選定や交換が可能になるのがメリットです。
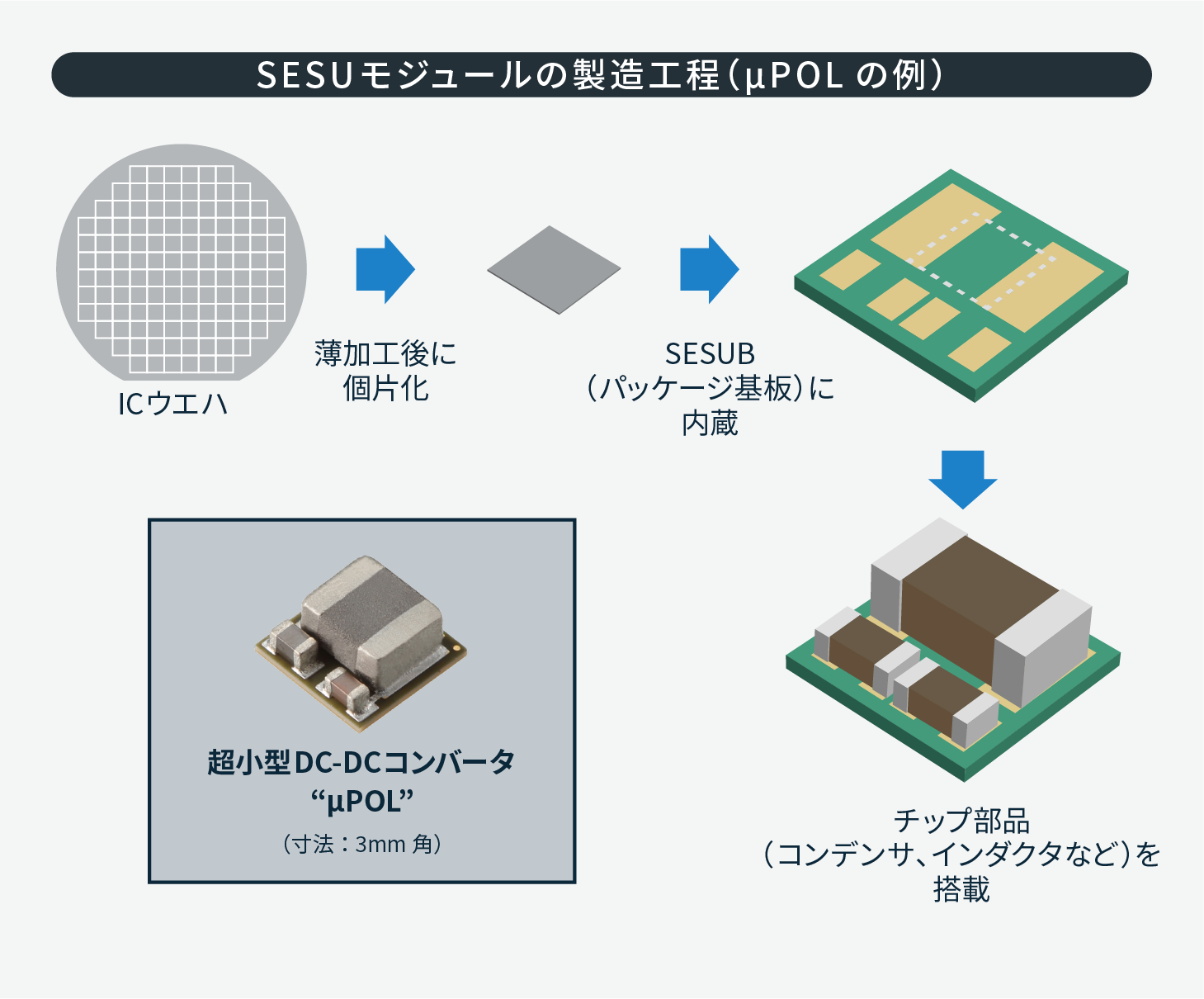
厚み300μmの基板内部にICチップを埋め込む
通常のビルドアップ工法は、コア基板の両面にビルドアップ層を積み重ねるのに対して、TDKのSESUBはIC埋め込み層にコア基板を使わずに加工することで、ICの厚みを100μm以下、基板の厚みを300μm(4層)以下という超薄型の基板を実現しています。
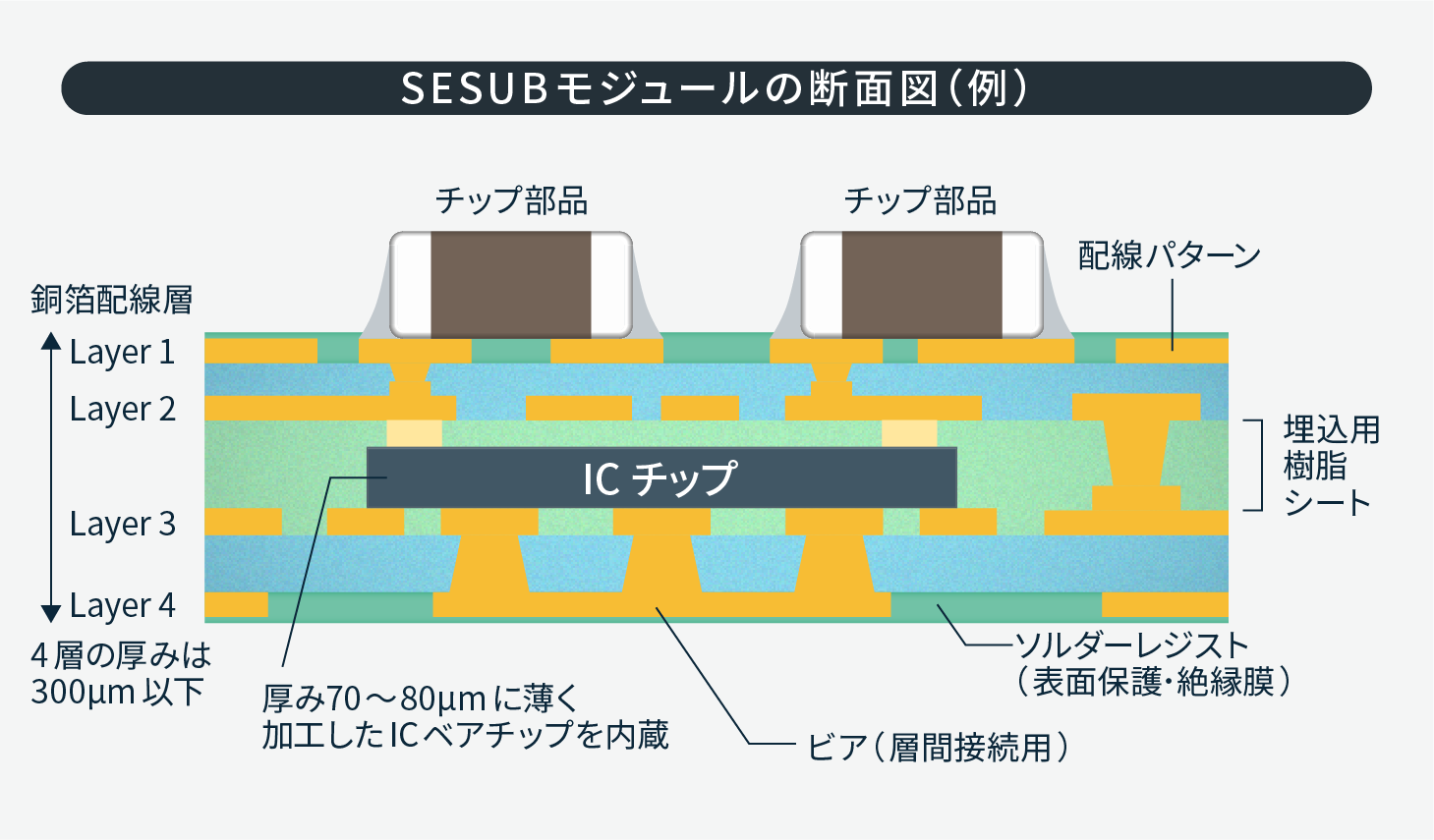
ICチップ直下のビアは、層間の電気的接続とともに、ICチップの発熱をマザーボード側に放熱する役割も果たす。
また、一般の部品内蔵基板では、コア基板あるいはプリプレグ(絶縁材シート)にキャビテイ(空洞)を設けてICチップなどを埋め込みますが、TDKのSESUBは、自社で開発した流動性にすぐれたシート材料(EOS:Embedding Organic Sheet)でICチップをラミネートし、加熱しながら圧着する工法を採用しています。このため、ボイド(気泡)などのない均質で信頼性の高い状態での埋め込みを可能としています。
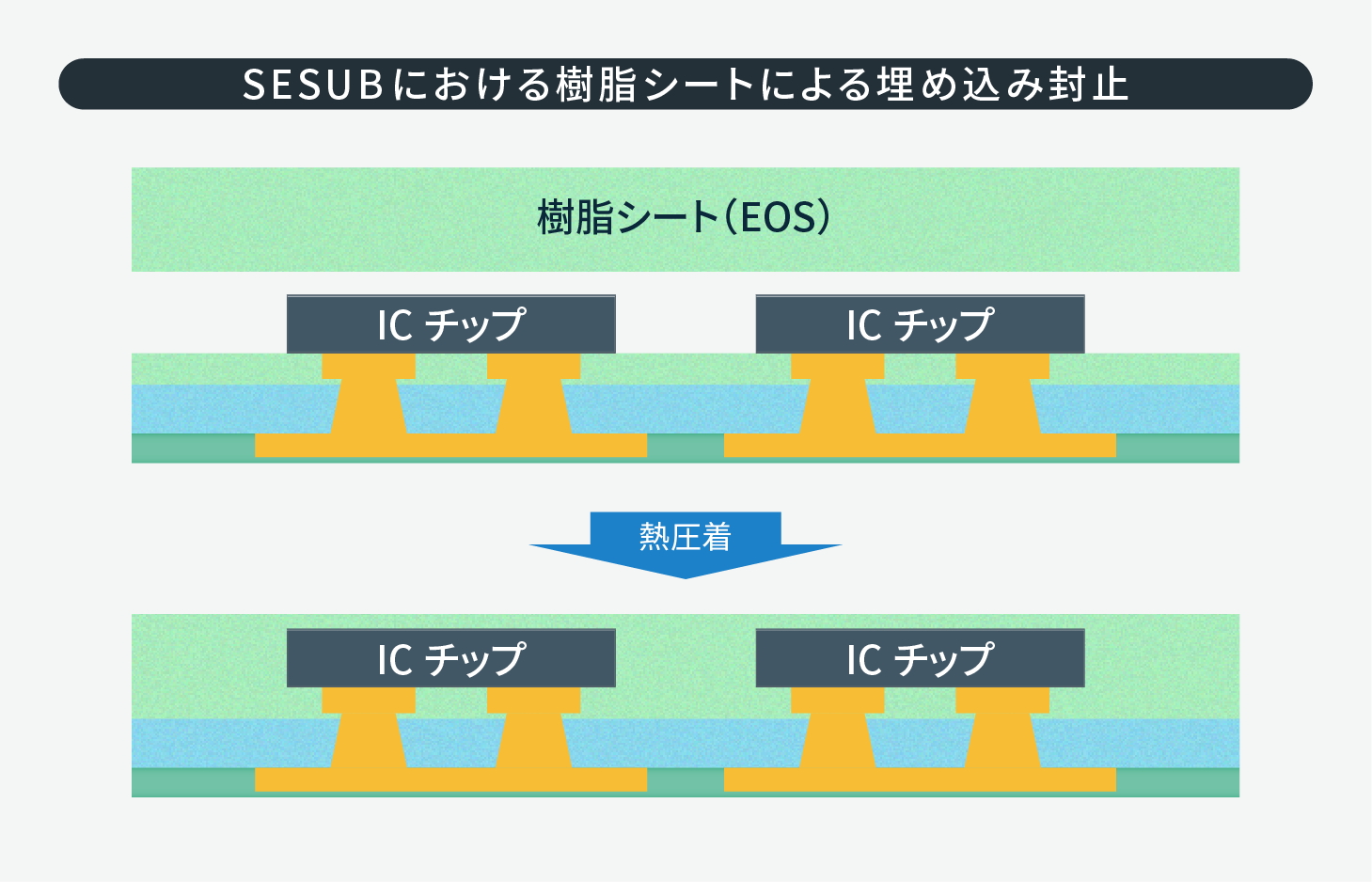
TDKのIC内蔵基板技術“SESUB”の特長
TDKのSESUBは、ビルドアップ工法を用いた部品内蔵回路技術の一種ですが、次のような多くの特長をもっています。
●省スペース化、モジュールの小型化
ICチップを薄く研削したベアダイ(ベアチップ)のままで基板内部に埋め込むので、パッケージICを表面実装する場合とくらべて、大幅な省スペース化とモジュールの小型化が実現します。
●すぐれた接続信頼性
埋め込まれるICチップは、はんだボールなどを用いないCu-Cu接続なので、長時間高温環境に置かれても、高い接続信頼性を維持します。
●低ESR・低ESL、すぐれたノイズ特性
ICチップを基板に埋め込むことで、周辺部品との接続経路を最短にでき、抵抗成分(ESR:等価直列抵抗)や寄生インダクタンス(ESL:等価直列インダクタンス)を減らし、信号品質の改善やノイズの低減に寄与します。
●高放熱特性
ICチップは発熱しますが、基板内に埋め込んだICチップ直下に放熱用ビアを形成することで、すぐれた放熱特性が得られます。
●樹脂シートによるICチップ封止
薄いICチップを特殊な樹脂シート(EOS)でラミネートして熱圧着することで、ボイド(気泡)などのない均質な状態での埋め込みが可能になります。
ウェアラブルデバイス、IoTデバイスなどに最適
TDKのSESUB技術を応用した小型モジュール製品の例を以下に示します。μPOLは、分散型電源システムの最終段や、5G通信のスモール基地局、エッジコンビューティングのサーバやストレージなど、広範な用途に適用できる超小型DC-DCコンバータです。
Bluetoothモジュールは、IoTデバイスやウェアラブルデバイスに搭載され、スマートフォンなどのハブ機器にデータを無線送信するための小型モジュールです。また、PMU(パワーマネジメントユニット)は、スマートフォンなどにおいて電源管理を担う小型モジュールです。いずれも数mm~10mm角程度の超小型モジュールです。
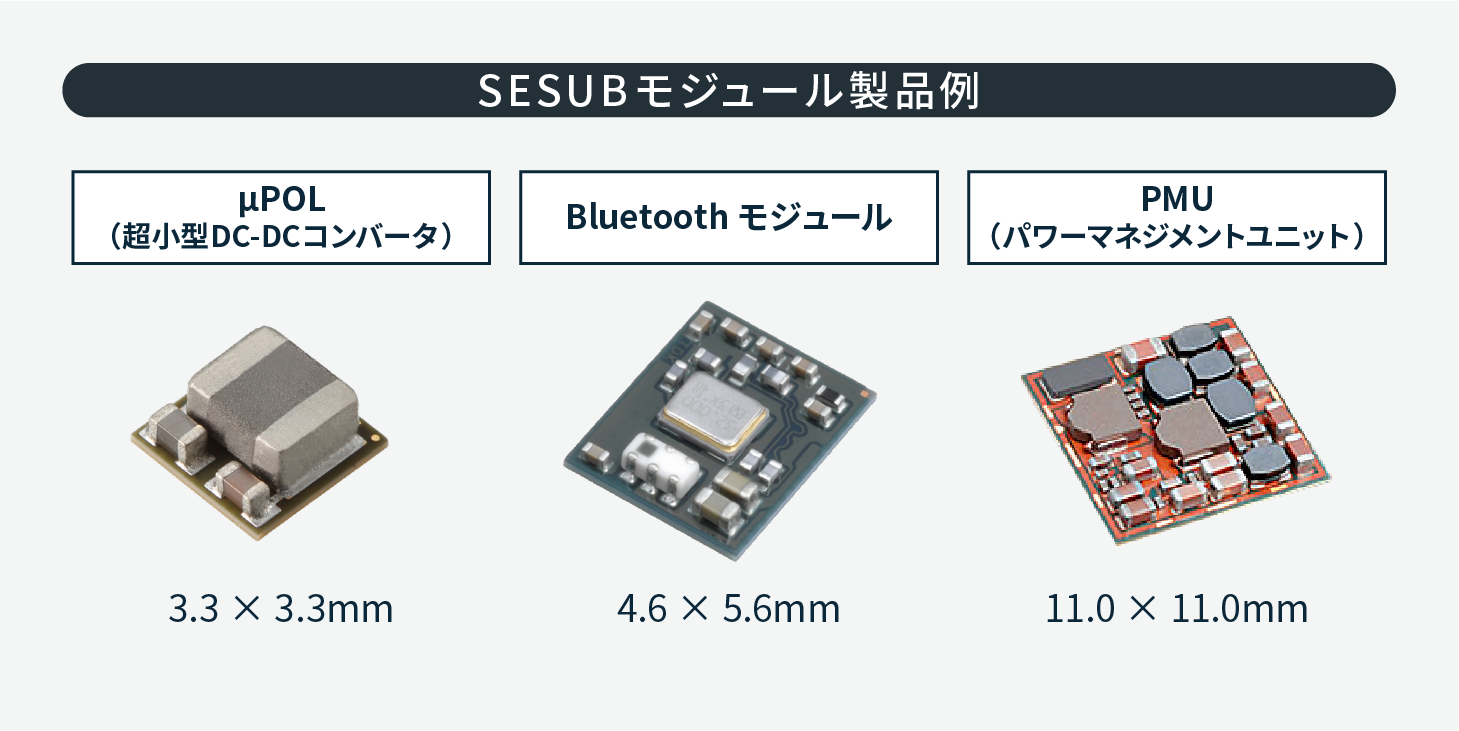
POL(Point of Load)とは「負荷の近辺」という意味。分散電源システムの最終段で使われるDC-DCコンバータをPOLコンバータという。
まとめ
TDK独自のIC内蔵基板技術であるSESUBは、約70~80μmにまで薄く研削したICチップ(ベアダイ)を4層のプリント基板内部に、特殊な樹脂シート材料でラミネートして埋め込む技術です。
SESUBはTDKが蓄積したさまざまなコアテクノロジーの結集により開発されました。ICチップを薄く研削する技術は、HDDヘッド製造におけるウエハ加工技術が活用されています。また、積層セラミックチップコンデンサ(MLCC)などの製造で培った電子材料技術やファイン積層技術、磁気テープなどで培った樹脂材料技術なども投入されています。
これらのコアテクノロジーを結集した高度な製品設計により、スマートフォンなどのモバイル機器はじめ、ウェアラブルデバイス、IoTデバイス、AR/VRデバイスなど、電子機器のさらなる小型・高速化・高機能化に向けた先進のソリューションとサービスを提供しています。
TDKは磁性技術で世界をリードする総合電子部品メーカーです