TDKのコアテクノロジー
Vol.12
パワーインダクタと「設計・製造技術」
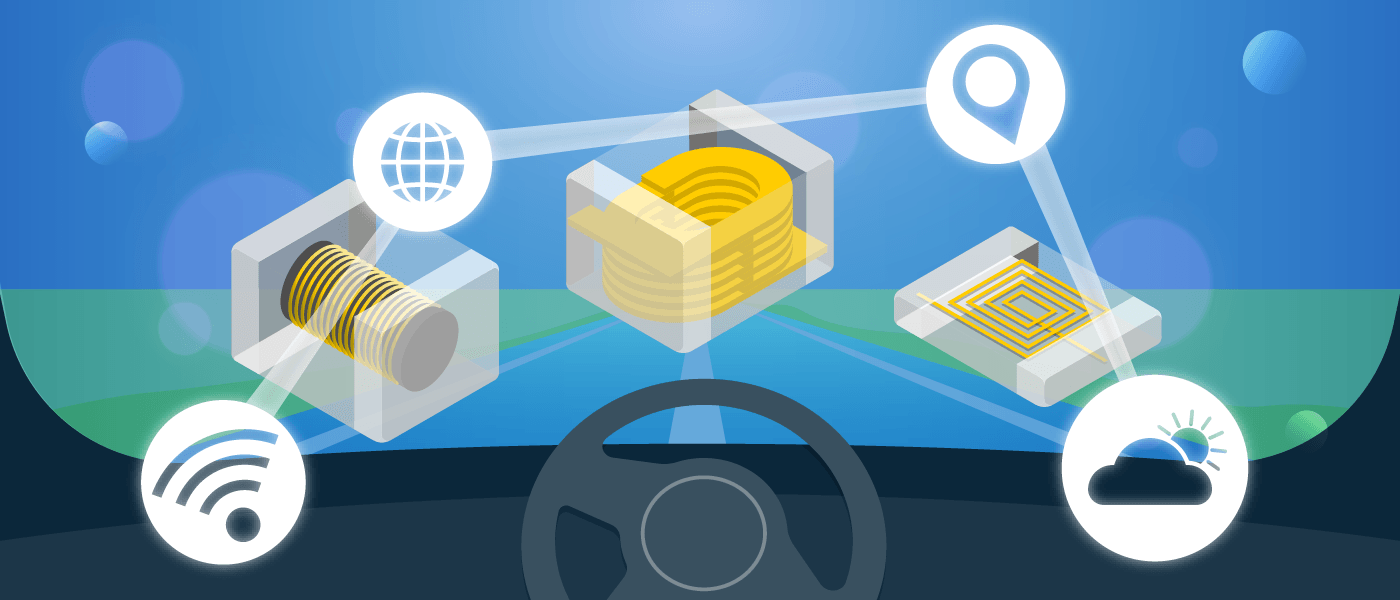
スマートフォンやタブレット、ノートパソコンなどのモバイル機器はじめ、自動車のECU(電子制御ユニット)など、電子機器に内蔵される電源回路(DC-DCコンバータ)には、「パワーインダクタ」と呼ばれる小型SMD(表面実装部品)タイプのインダクタ(コイル)が使われています。本記事ではパワーインダクタの機能や役割、および様々な特性を作り出す設計・製造技術を中心にご紹介します。
DC-DCコンバータにおけるパワーインダクタの役割
パワーインダクタは、パワーコイル、パワーチョーク、電源系インダクタなどとも呼ばれ、直流入力電圧を必要な出力電圧に変換するDC-DCコンバータの主要部品のひとつです。パワーインダクタには巻線型、積層型、薄膜型があり、大電流対応のDC-DCコンバータでは巻線型が主流です。巻線型にはフェライトコアを用いたタイプと、金属磁性材料を用いた金属一体成型あるいはメタルコンポジット型と呼ばれるタイプがあります。
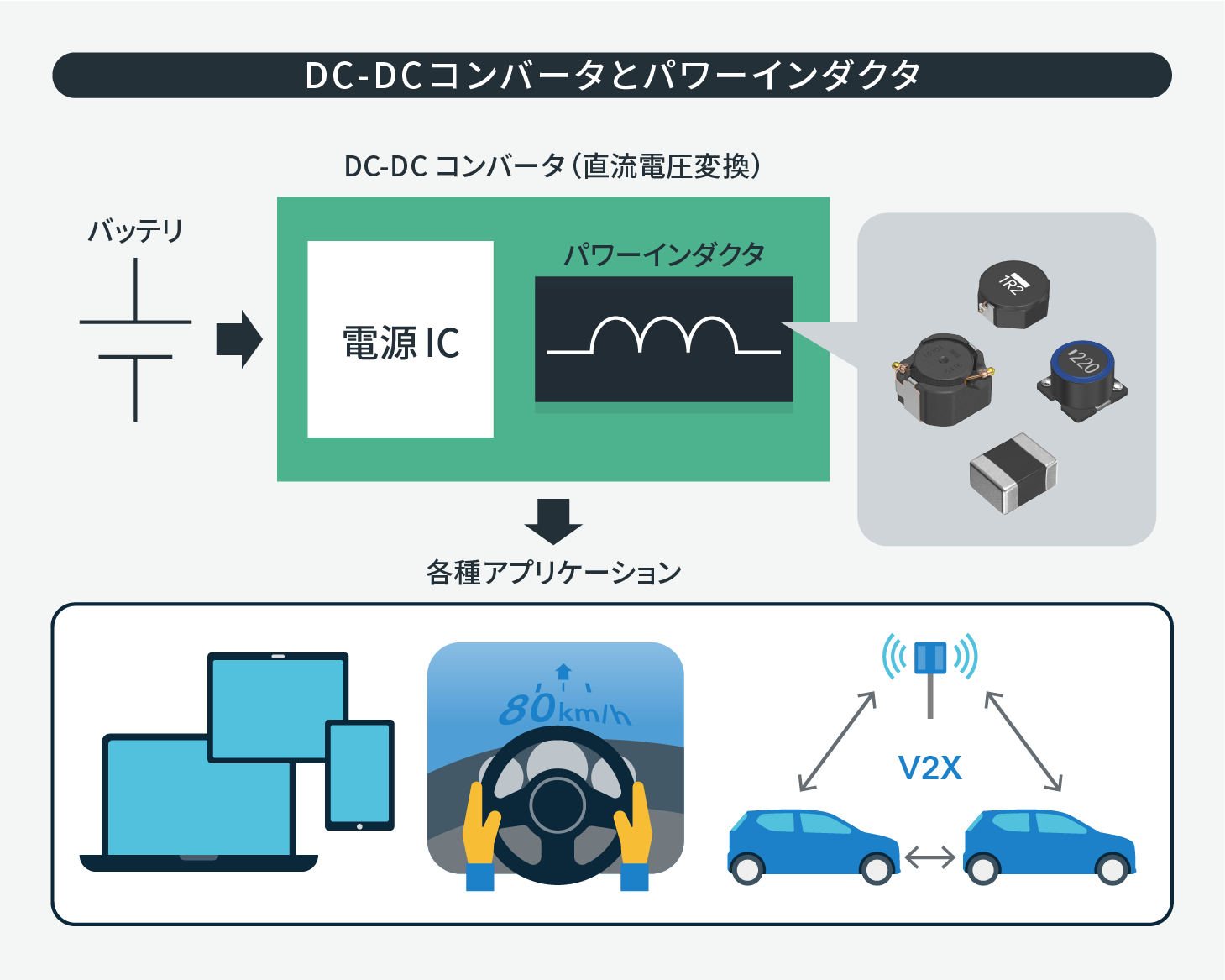
パワーインダクタには、巻線型、積層型、薄膜型がある。いずれも数mm角ほどの小型SMD(表面実装部品)
インダクタやトランスなどは、コイルの電磁誘導(Electromagnetic induction)を利用していることから、インダクティブ・デバイスとも呼ばれます。
インダクタは直流電流をスムーズに流しますが、交流電流のような変化する電流に対しては、電磁誘導における自己誘導作用により、変化を阻止する方向に逆起電力を発生して誘導電流を流し、抵抗のように作用します。このとき、インダクタは電気エネルギーを磁気エネルギーとして蓄えます。これを利用したのがパワーインダクタです。
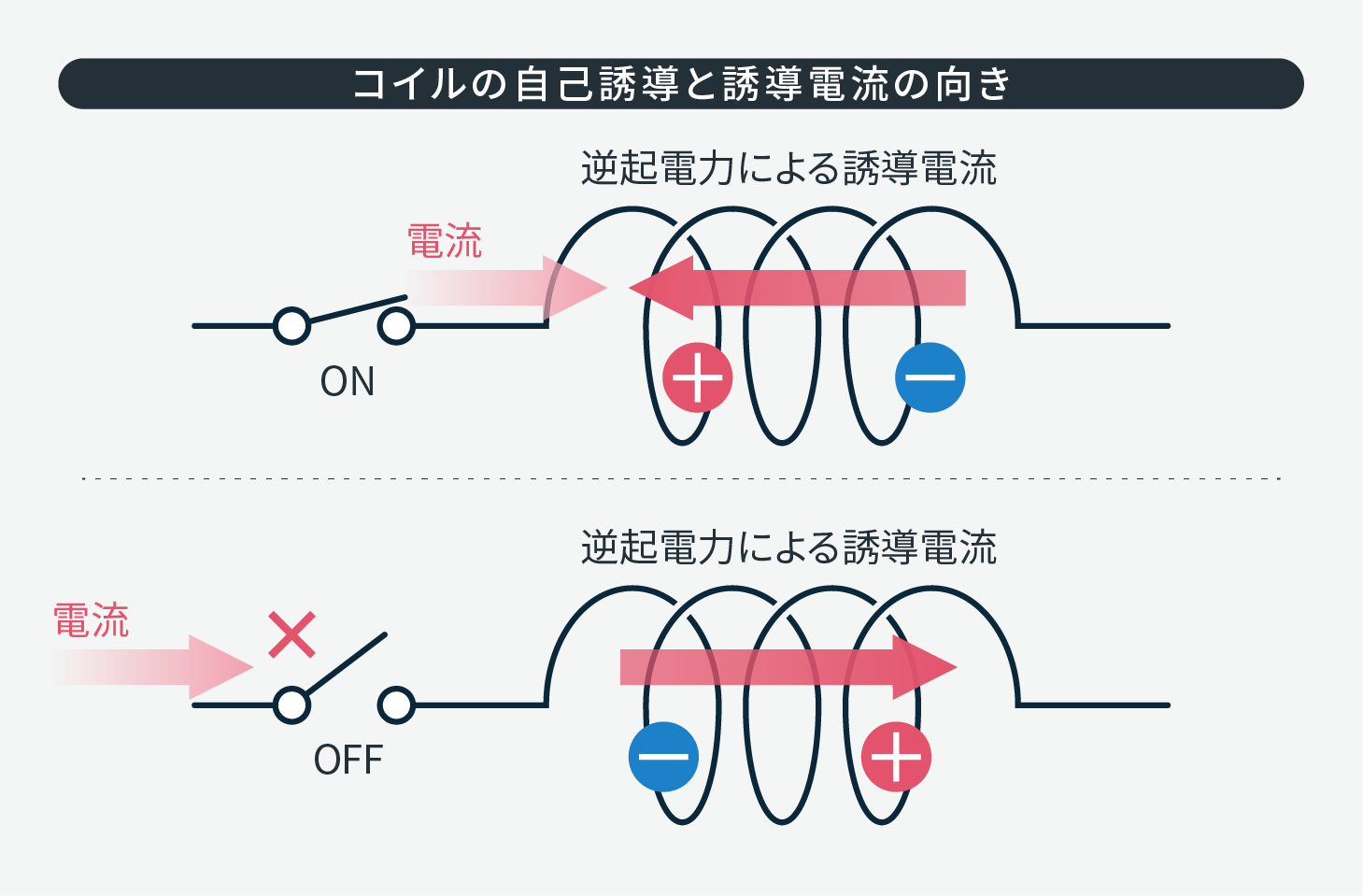
スイッチのON/OFFや交流電流に対して、あたかも電流の流れを詰まらせる(choke)ように振る舞うことから、チョークコイルとも呼ばれる。
電流をパルス状にして電圧変換するスイッチング電源
最もシンプルなスイッチング電源であるチョッパー方式の降圧型DC-DCコンバータの基本回路を以下に示します。
スイッチング素子(トランジスタやMOSFETなど)により、入力直流電圧を高速ON/OFFしてパルス化して送ると、パワーインダクタはON時にエネルギーを蓄え、OFF時にエネルギーを放出します。これをコンデンサとともに平滑すると、ON/OFFの時間比(デューティ比)に応じた電圧に降圧されて安定した直流電圧となります。これが降圧型DC-DCコンバータの原理です。いわば電流を細切れ(chop)にしてからつなぎ合わせるため、チョッパー方式と呼ばれています。
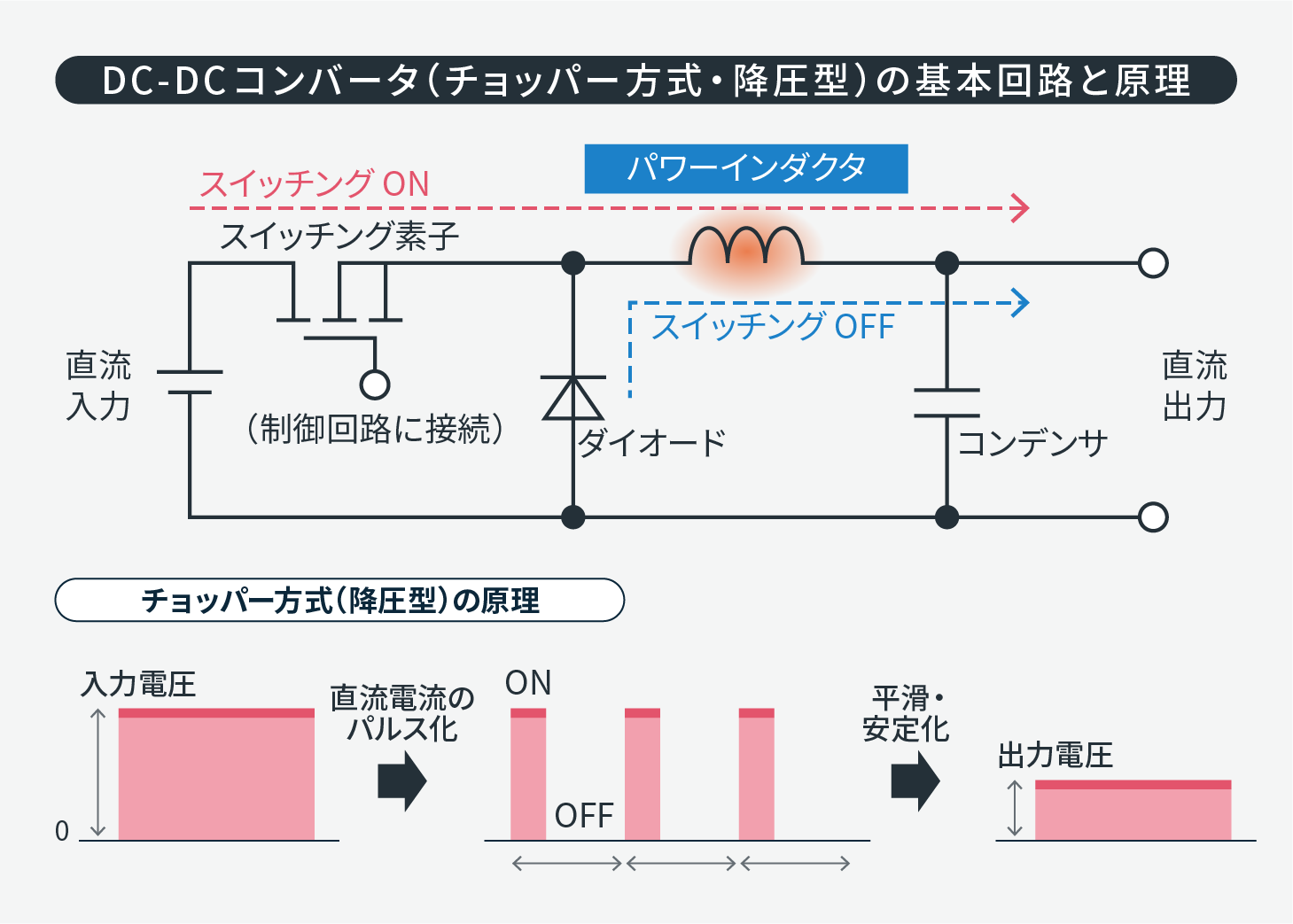
スイッチング素子(トランジスタやMOSFET)により、スイッチON時にはパワーインダクタはエネルギーを蓄え、スイッチOFF時には蓄えられたエネルギーを放出する。スイッチングのデューティ比(ON時間/スイッチング周期)に応じて、一定電圧の安定した直流に降圧される。
コイルの基本性能を表すインダクタンス
コイルの性能を表すパラメータは様々ですが、最も基本的なのはインダクタンス(L)で、コイルが蓄えるエネルギーの大きさはインダクタンスに比例します。
コイルの大きさや巻数とインダクタンスには次のような関係があります。コイル径を大きくすればインダクタンスは高まりますが、サイズは大きくなってしまいます。また、同じコイル径の場合、巻数を多くすることでインダクタンスは高まりますが、細い銅線を使うと直流抵抗(Rdc)が増して、銅損と呼ばれるロス(発熱損失)が大きくなります。かといって、直流抵抗を下げるために太い銅線を用いると体積は増加してしまいます。
インダクタンスを高めるうえで最も効果的なのは、フェライトまたは軟磁性の金属材料をコアに用いることです。コアは多くの磁束を集め、インダクタンスは空芯コイルの数十~数千倍以上にも高まります。
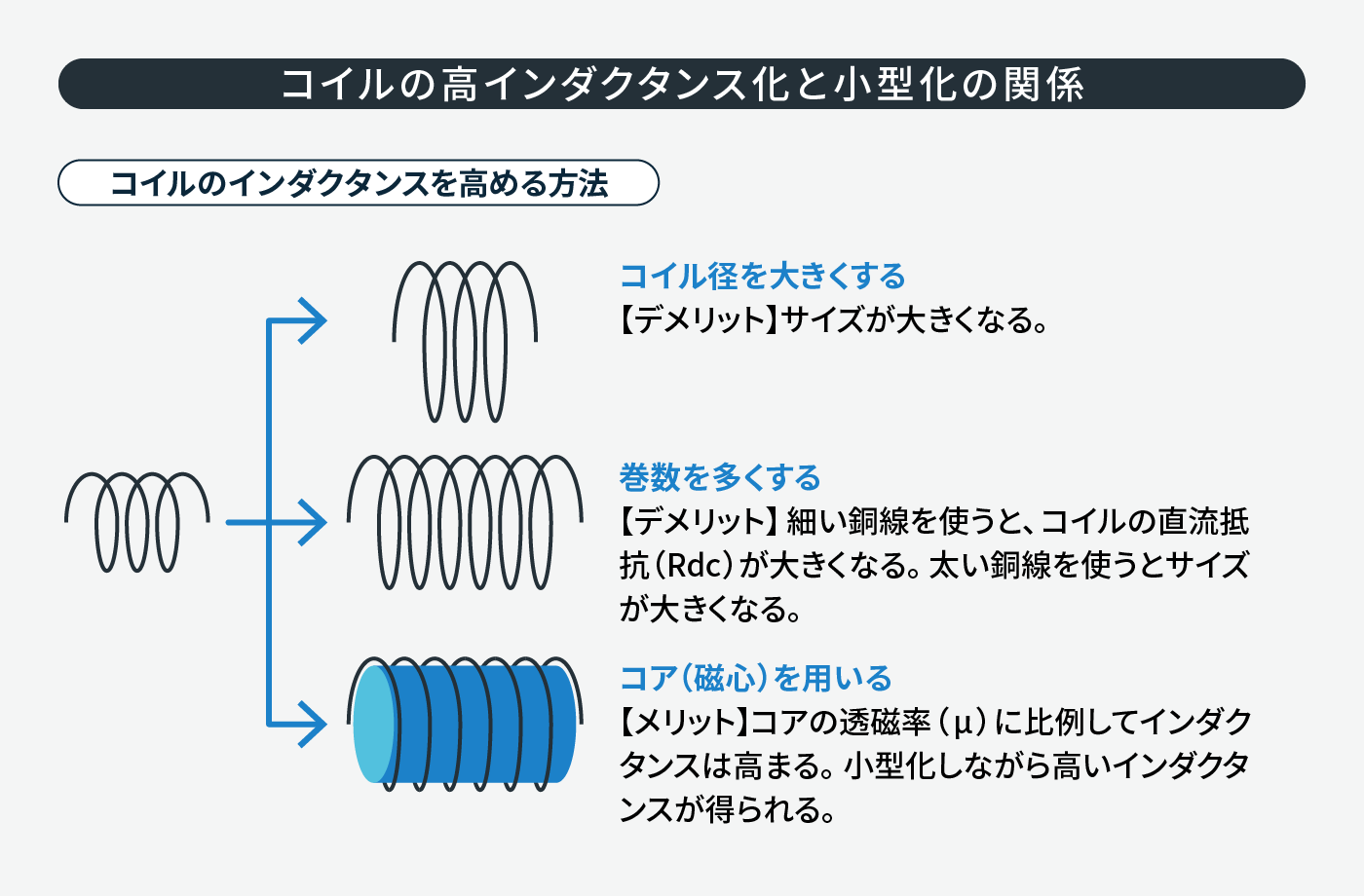
コア材料にはフェライトもしくは軟磁性の金属材料が用いられる。
コア材料とパワーインダクタの特性
電磁石やモータ、電源トランスなどのコアにケイ素鋼などの鉄系磁性材料が用いられるのは、鉄は高い飽和磁束密度(Bs)を有して、より多くの磁束を集めるからです。
しかし、高周波の電流に対しては、鉄系磁性材料は鉄損と呼ばれるコアロスが大きくなって使えません。そこで、軟磁性の金属粉末の表面を絶縁被膜で覆って、バインダー(結合剤)とともに圧縮成形したコアが用いられます。これはダストコアとか圧粉磁心と呼ばれます(センダストは代表的なダストコア材料です)。
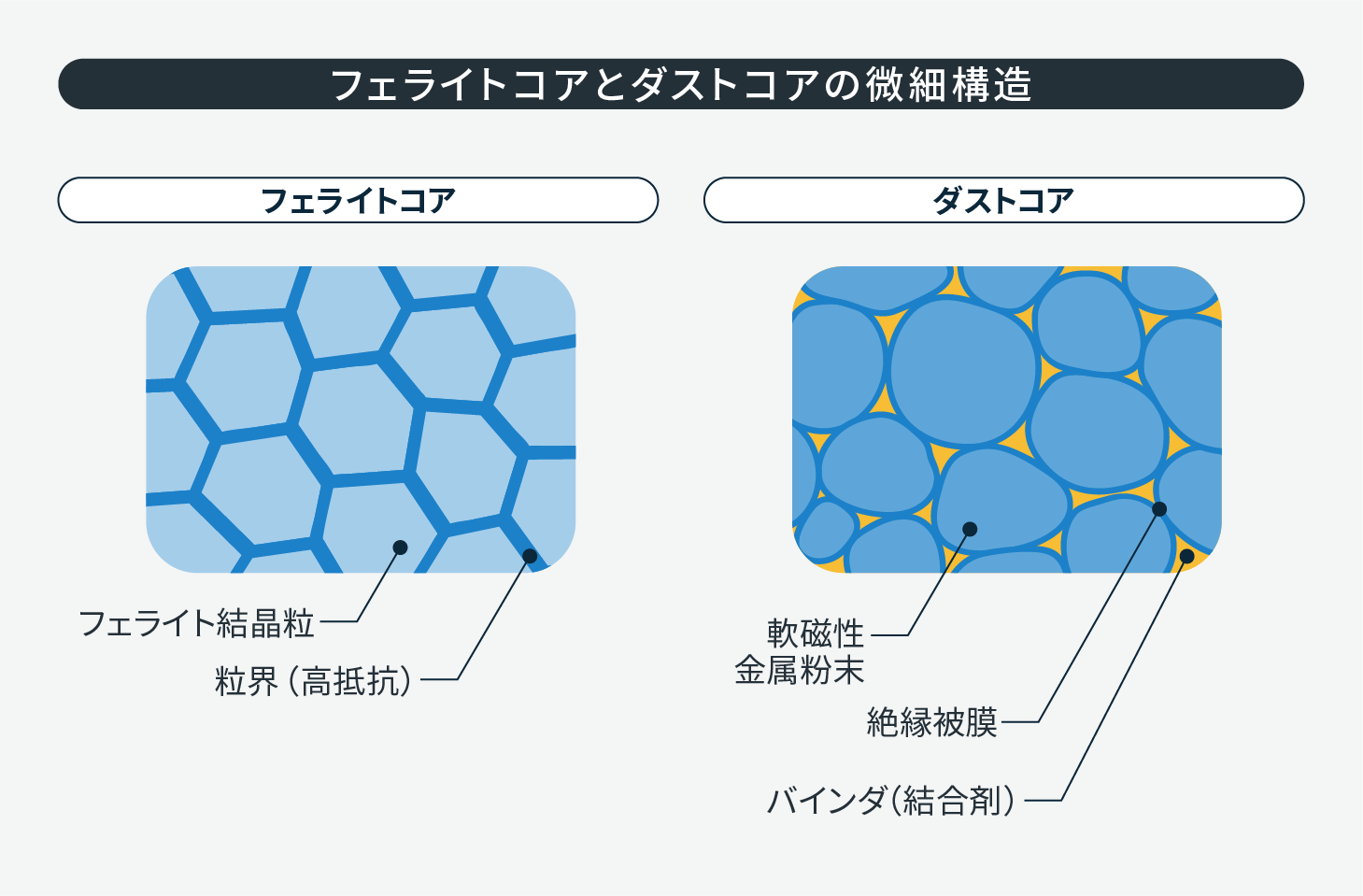
フェライト結晶粒どうしの境界を粒界という。粒界は微量添加物などが析出して高抵抗であるため、高周波におけるコアロスが少ない。軟磁性金属粉末はそのままでは低抵抗なので、表面を絶縁被膜で覆って圧縮成形する。
コアを用いることでインダクタンスは著しく高まりますが、その能力には限界があります。 コアが磁気飽和に達する磁束密度の上限値のことを飽和磁束密度(Bs)といいます。飽和磁束密度を超えると、コイルは空芯状態となって電流が暴走的に流れ、発熱によりコイルが破損するなどの事故を起こす危険性があります。したがって、パワーインダクタは定格電流以下で使用することが求められます。
コア材料の透磁率と直流重畳特性
コア材の直流重畳特性もパワーインダクタの性能に大きく関わります。直流重畳特性とはコイルに流す直流電流を高めていくと、磁気飽和が始まるにつれ、インダクタンスが低下する性質のことです。
下図に示すように、金属磁性材料はフェライトよりも直流重畳特性にすぐれるため、主に大電流対応のパワーインダクタに使用されます。フェライトは磁気飽和に近づくと、インダクタンスは急激に落ち込む性質がありますが、磁束の通しやすさを表す透磁率(μ)が高いので、同じコア体積で金属磁性材料よりも高いインダクタンスが得られます。このため、大電流用途のインダクタのコア材には金属磁性材料、高インダクタンス用途にはフェライトが使い分けられています。
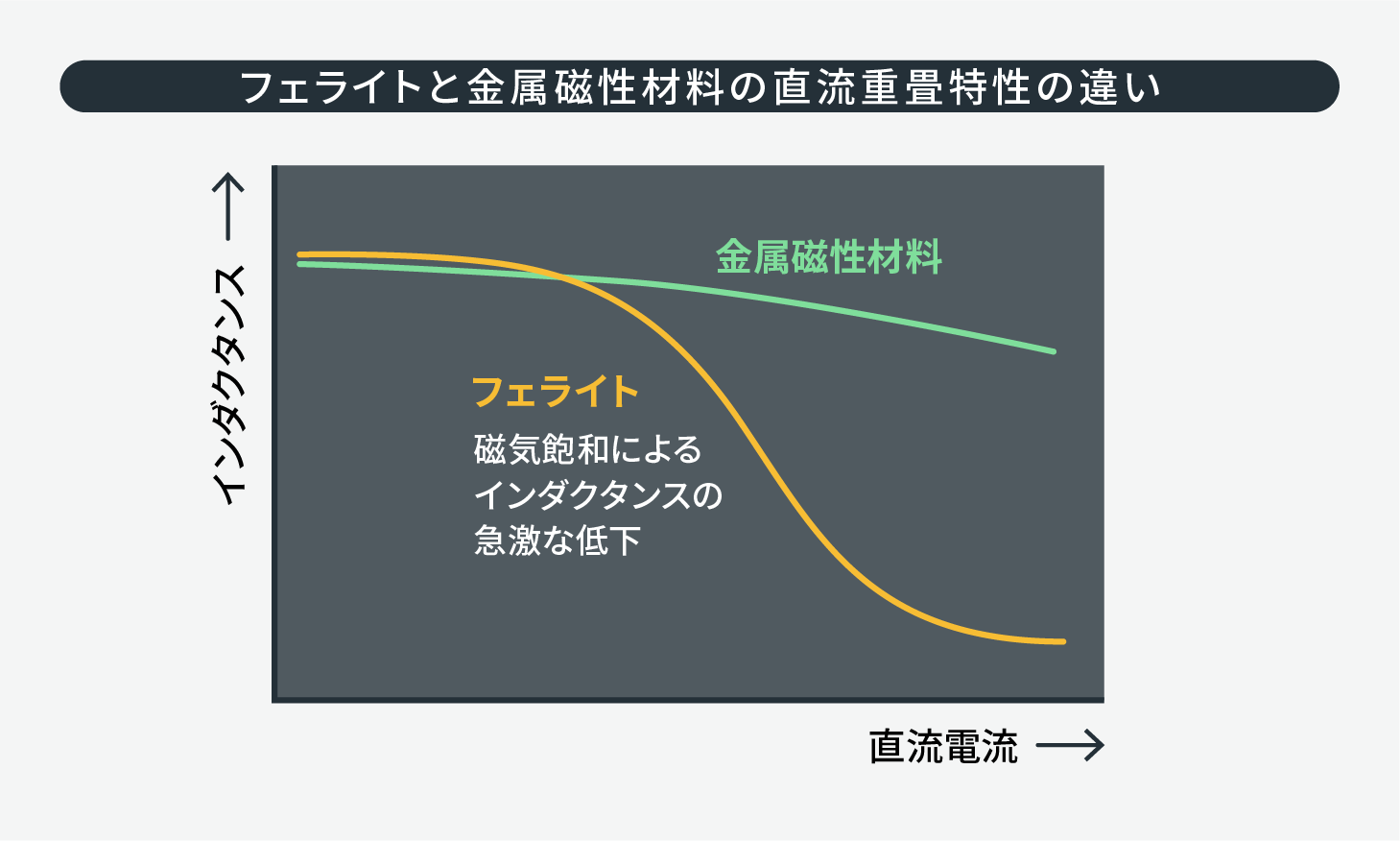
コイルに流す電流を高めていくと、やがてコアは磁気飽和してインダクタンスが低下するようになる。これを直流重畳特性という。金属系磁性材料はフェライトと比べて直流重畳特性にすぐれるため、大電流対応のパワーインダクタのコアとして使われる。
フェライトコアと金属磁性材料コアによるパワーインダクタの特性の違いを以下にまとめました。これらの特性は、電流の大きさや温度によって変化します。たとえば、巻線の太さや巻数により直流抵抗(Rdc)値が変わると、発熱の度合も異なり、インダクタンスも変化します。また、電流増大にともなう温度上昇により、コアの透磁率(μ)や飽和磁束密度(Bs)も変化します。こうした特性の多くは、互いにトレードオフの関係にあるため、用途に応じて最適のパワーインダクタを選択することが必要です。
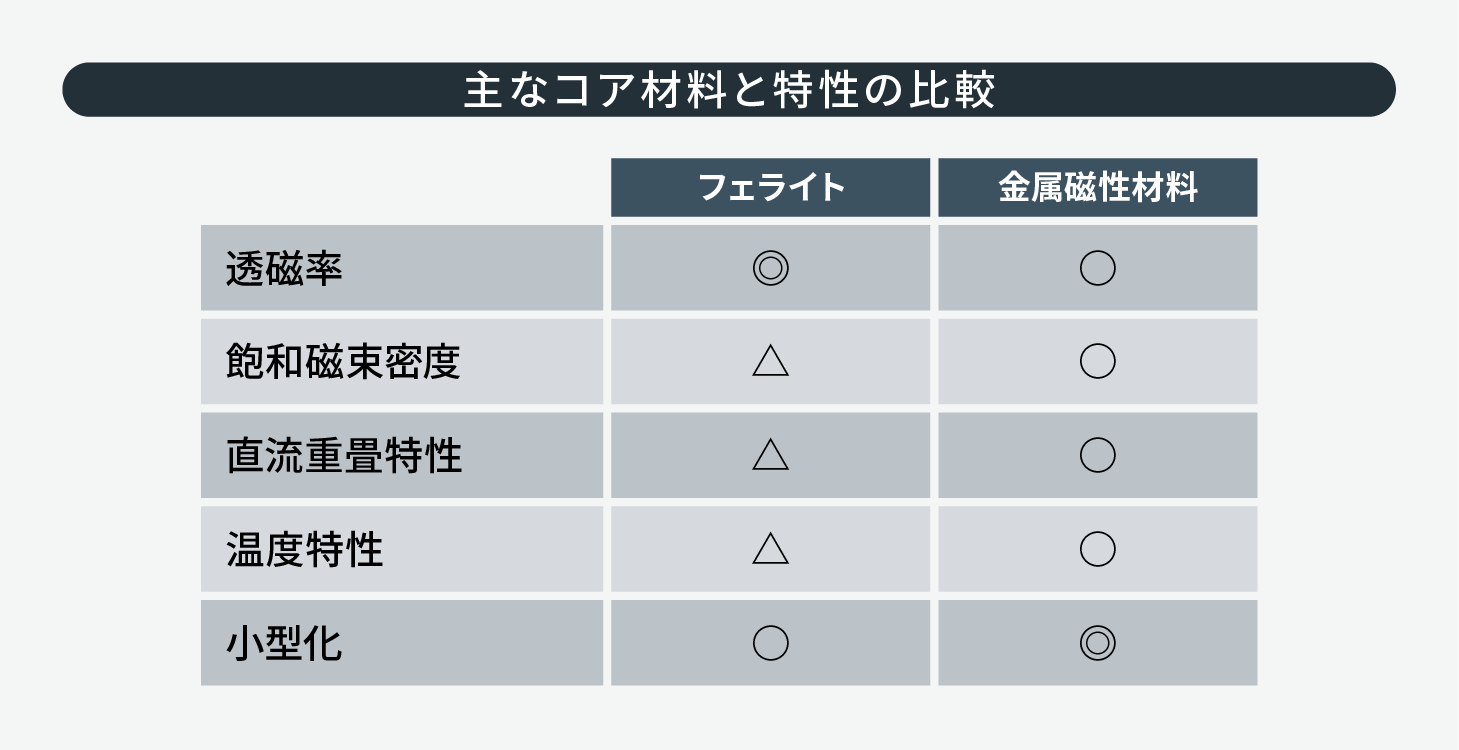
◎:非常に良い 〇:良い △:普通~やや劣る
漏れ磁束を低減するための磁気シールド構造
パワーインダクタは、磁気シールドの違いにより開磁路構造と閉磁路構造に大別されます。ドラムコアに巻線をほどこしただけの開磁路構造では、漏れ磁束が多くて周囲と磁気的に結合して干渉したり、ノイズの原因となったりします。そこで、リングコアなどでドラムコアを囲ったり、金属一体成型タイプのようにコイル全体を金属磁性材料の粉末の中に閉じ込めたりします。これを閉磁路構造といいます。
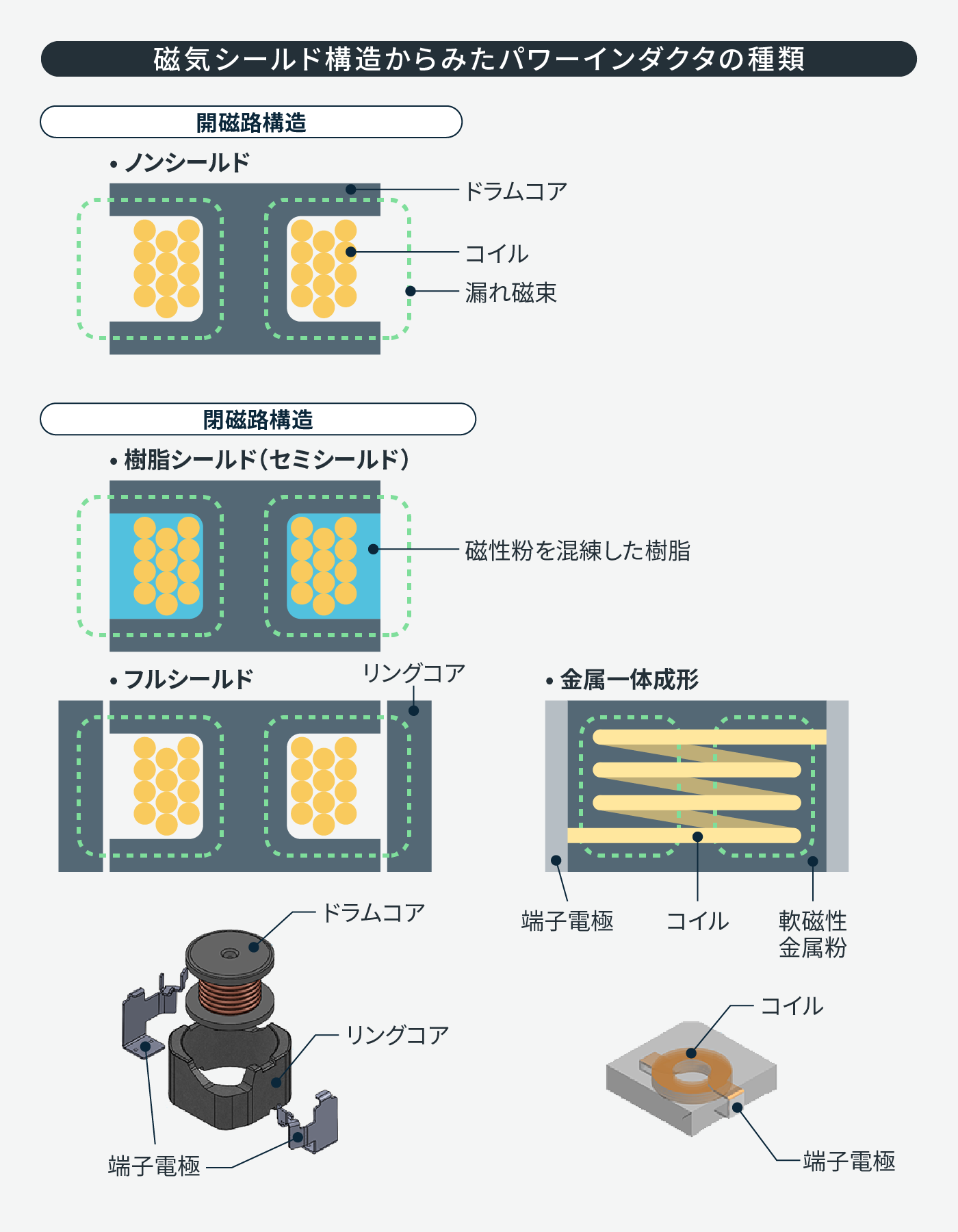
閉磁路構造では、金属一体成型>フルシールド>樹脂シールド(セミシールド)の順に、磁気シールド効果が高い。
自動車のECUでは多種多様なパワーインダクタが活躍
xEV(電気自動車)の普及、ADAS(先進運転支援システム)や自動運転の導入などにより、自動車のECU(電子制御ユニット)の数は増加傾向にあり、内蔵されるDC-DCコンバータの小型化や信頼性がますます強く求められています。ECUにはさまざまなタイプがありますが、その基本構成を以下に示します。

ECUの電源回路では補機バッテリからの入力電圧(12Vなど)を、1次DC-DCコンバータでいったん5Vなどの中間電圧に降圧してから、2次DC-DCコンバータでCPU、モータ/アクチュエータ、カメラ/ディスプレイなどの動作電圧(3.3V、1.8V、1.0Vなど)に降圧する2段構成となっています。2段構成をとるのは、入力電圧と出力電圧の降圧比が高すぎると、変換効率が悪くなるからです。
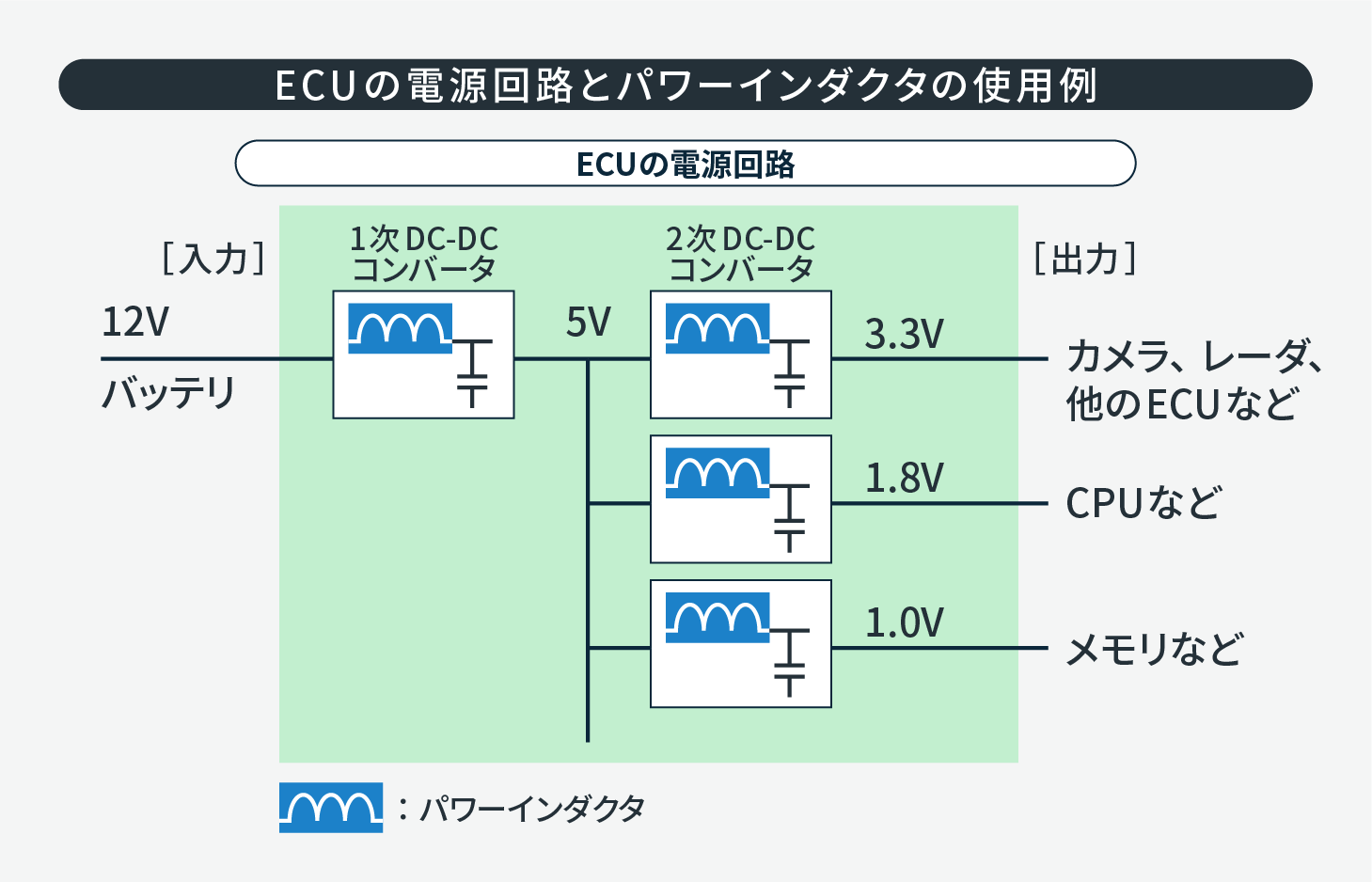
ECUのDC-DCコンバータには、小型化や効率化を図るため、用途に応じた最適のパワーインダクタが選択される。
パワーインダクタのコアロスの種類
コイルのコアサイズは、DC-DCコンバータのスイッチング周波数とも関係します。周波数が高くなるほど必要なインダクタンス値は小さくなるため、コアの断面積は小さくてすむからです。しかし、周波数が高くなるにつれコアロス(発熱損失)も大きくなります。
ロスには直流電流による損失と、交流電流による損失があります。比較的周波数の低い領域(約100kHz以下)では、巻線の直流抵抗(Rdc)による損失(銅損)がメインですが、周波数が100kHzを超えると、交流損失(ヒステリシス損や渦電流損)のほうが支配的になります。ヒステリシス損とは、コアに交流磁界を加えたときに生じるエネルギー損失のことで、S字ループを描く磁化曲線の面積に比例します。渦電流損とは、交流磁界によりコア材料の内部に誘導される渦状の電流によるエネルギー損失のことです。
とくに高周波領域における渦電流損は周波数の2乗に比例し、損失は発熱となって特性をさらに低下させるため、高周波領域でコアロスが小さく、かつ温度特性にもすぐれたコア材料が求められます。
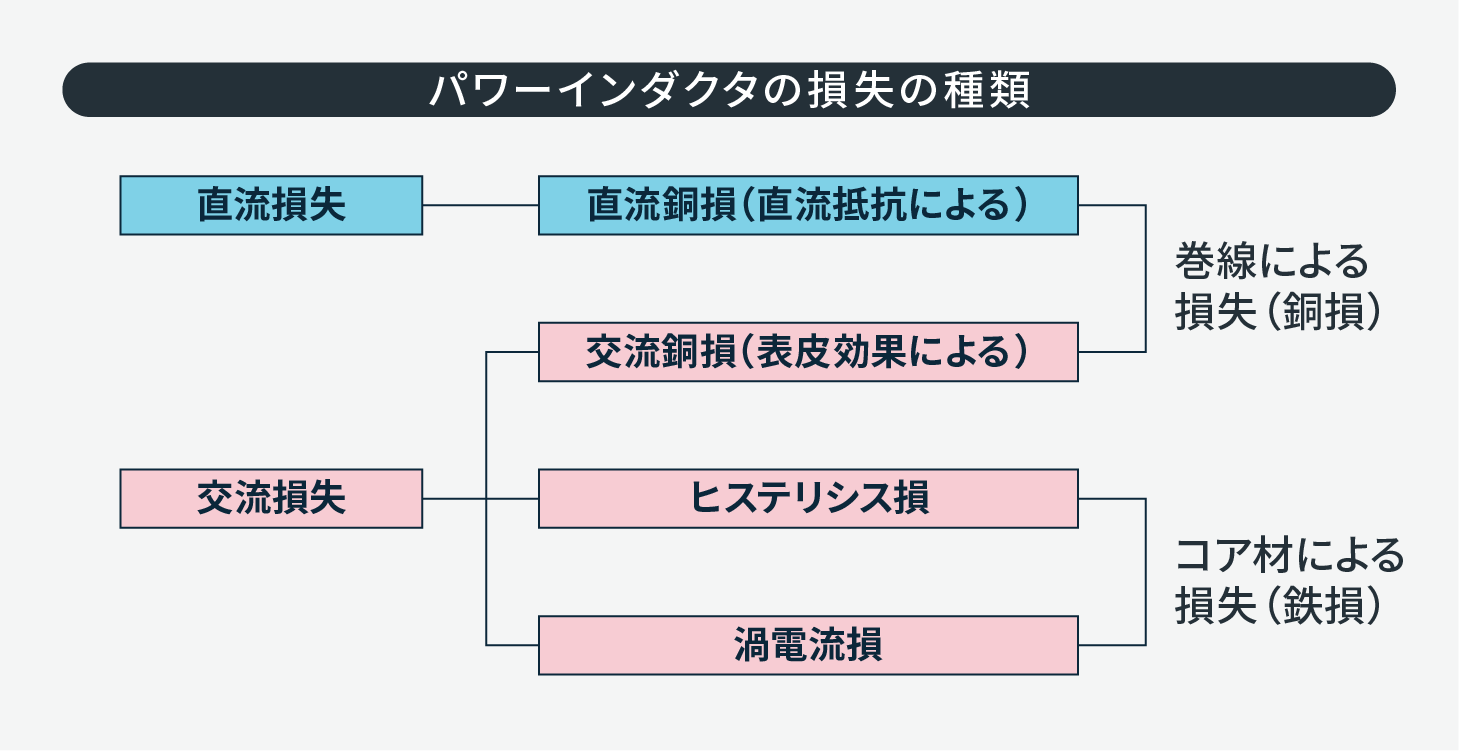
フェライトは高抵抗なので渦電流損が小さい。ダストコアでは金属磁性粉の表面に絶縁被膜で覆って抵抗を高め、渦電流損の低減を図っている。
高周波化に対応したパワーインダクタ
初期のスイッチング電源の動作周波数は数10~100kHzでしたが、その後、500kHz前後まで高周波化が進み、近年はAMラジオの周波数(約500kHz~1.7MHz)との干渉を避けて、いっきに1.8~2MHz以上の高い周波数にも対応するようになっています。
TDKでは2MHz以上の高周波に対応した高信頼性のパワーインダクタ(HPL/TFM/BCLシリーズ)を開発し、ECUのDC-DCコンバータ用として提供しています。HPLシリーズは、画像処理用プロセッサなどの大電力ECU、高インダクタンス・低電流に対応したBCLシリーズはセンサ系やボディ系などの小電力ECU、TFMシリーズはその中間領域のECUのDC-DCコンバータ用として最適パフォーマンスを発揮します。
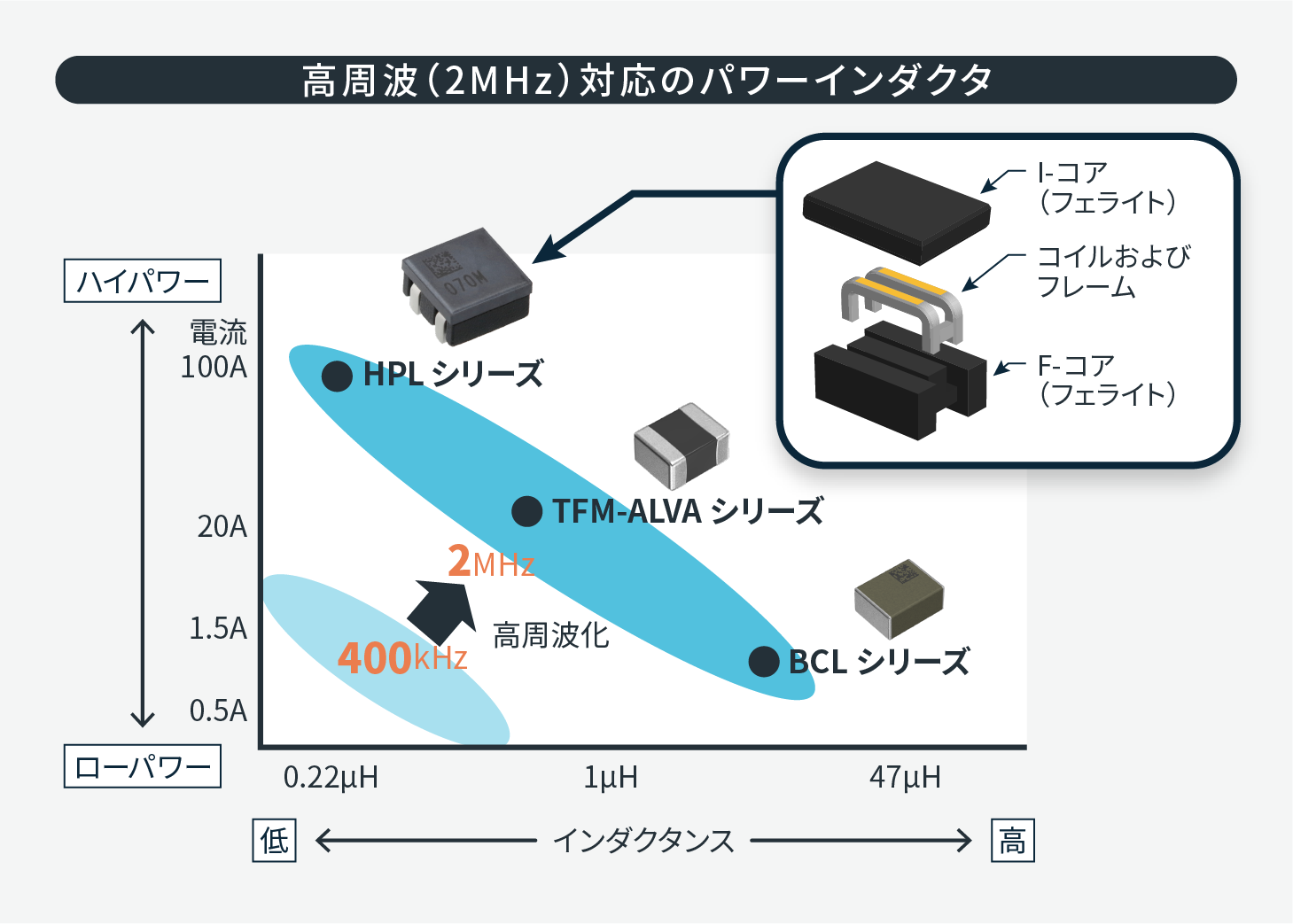
HPLシリーズは、フェライトのI-コアとF-コアで銅バーコイルをはさんだフレームフォーミング構造。外部端子と接合レスなので、耐振動性にすぐれ、オープン(断線)などのリスクを低減できる。
用途に応じた多種多様なパワーインダクタをラインアップ
パワーインダクタはDC-DCコンバータの性能を左右する重要な電子部品です。TDKは巻線型、積層型、薄膜型の各種製品を豊富にラインアップしています。
パワーインダクタの設計の難しさは、インダクタンス、直流抵抗(Rdc)、直流重畳特性、温度特性、定格電流、周波数特性などの多くが、互いにトレードオフの関係にあることによるものです。したがって、サイズや磁気シールド構造、コストなどとともに、総合的な観点から、用途に応じた最適なパワーインダクタを選択することが重要です。
とくに車載用途においては、エンジン車とxEVでは環境温度の要求値が大きく異なるとともに、信頼性の要求時間は3,000時間にもなると予測されています。TDKは磁性材料技術や設計技術、生産技術などのコアテクノロジーと総合技術力を結集して、オートモーティブの未来をサポートする先進のパワーインダクタを提供してまいります。
TDKは磁性技術で世界をリードする総合電子部品メーカーです