TDKのコアテクノロジー
Vol.7
エレクトロセラミックスと「成形・焼成技術」
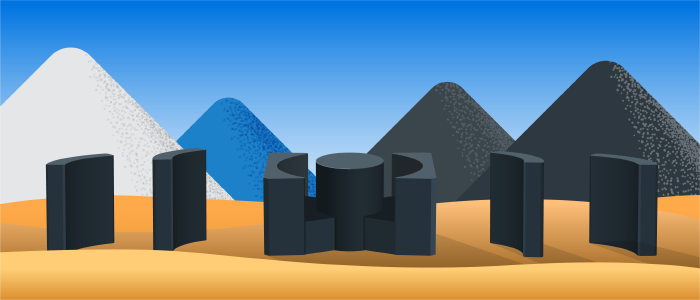
研究・開発によって生まれた試作品を、実用的な量産品とする製造工程に関わるのが各種プロセス技術です。エレクトロセラミックス製品においては、素材の持ち味を最大限に引き出すためのプロセス技術として、高度な「成形技術」と「焼成技術」が求められます。粉末の原料がどのようにして多彩な機能をもつエレクトロセラミックスへと変身を遂げるのか?フェライトコアやフェライトマグネットの製造工程を解説しながら、成形技術・焼成技術の奥深い世界をご紹介します。
セラミックナイフは宝石のルビーやサファイアと同成分
見た目も性質もまったく異なる製品が、同じ原料であることに驚かされることがあります。たとえば、人工ルビーや人工サファイアとセラミックナイフは、ともにアルミナ(酸化アルミニウム:Al2O3)の粉末が原料です。しかし、セラミックナイフなどのアルミナセラミックス製品は宝石のような透明性をもちません。この違いは、人工ルビーや人工サファイアはアルミナの単結晶体であるのに対して、アルミナセラミックスは多結晶体であることによるものです。
単結晶とは結晶格子を構成する最小単位(単位胞という)が、整然と連続して立体的に配列した物質のことです。一方、セラミックスは微細な単結晶の粒子が集合した多結晶体です。アルミナセラミックス製品が白っぽくて不透明なのは、多数の結晶粒の表面で光が散乱するからです。
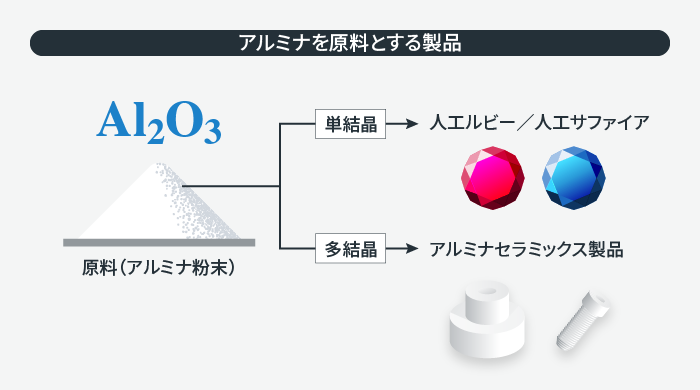
セラミックス製品は多結晶体であるため一般に透明性はもたない。
人工ルビーと人工サファイアは、1902年、初の人工宝石としてフランスの化学者ベルヌーイにより合成されました。高純度のアルミナ粉末を酸水素炎の高温(2,000℃以上)で溶融して、ゆっくり冷却させていくと単結晶が成長することを利用したものです。この製法はベルヌーイ法と呼ばれ、以後、さまざまな単結晶育成法が開発されました。
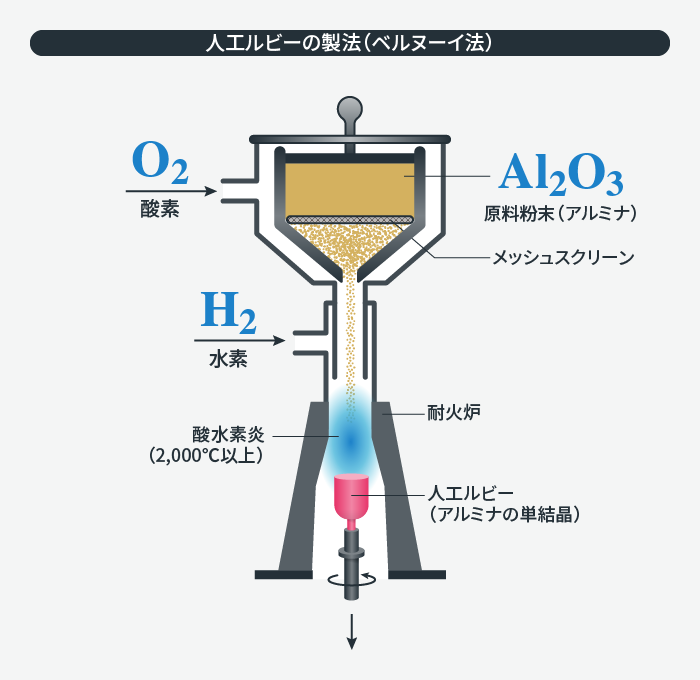
純粋なアルミナ単結晶は無色透明で、微量のクロム(Cr)を添加すると赤色のルビーに、微量の鉄(Fe)やチタン(Ti)を添加すると青色のサファイアになる。
焼結型フェライトのメリット
エレクトロセラミックスのひとつである「フェライト」も、粉末原料(酸化鉄など)を溶融して単結晶として育成することができます。たとえば、Mn-Zn(マンガン亜鉛)フェライトの単結晶は、磁気特性や耐摩耗性にすぐれるなどの性質があり、VTR(ビデオテープレコーダ)の全盛時には、磁気ヘッドのコア材料として多用されました。
しかし、これは特殊な応用例で、トランスやインダクタのコア材料としては、粉末原料を混合・成形・焼成して製造される、多結晶の焼結型(セラミックス)フェライトが利用されます。凹凸や曲面のある複雑形状に成形でき、小型から大型製品まで低コストで量産できるのが、焼結型のフェライトのメリットだからです。
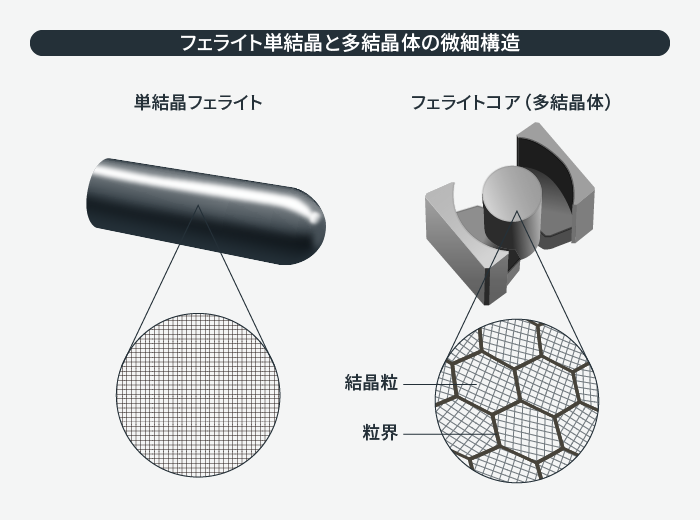
拡大図のメッシュ模様は、結晶格子の配列方向を表す。
上図のように、単結晶の結晶格子の配列はどの部分をとっても均一で、同じ方向を向いています。一方、多結晶体は多数の結晶粒の集合体であり、それぞれの結晶粒の結晶格子はランダムな方向を向いています。結晶粒どうしの境界を粒界(りゅうかい)といいます。多結晶体であるフェライトコアが示すさまざまな電磁気的な特性は、フェライト結晶粒の特性と粒界の特性の相乗作用によるものです。
フェライトコアの製造プロセスにおける成形技術や焼成技術は、結晶粒の大きさや粒界の形成などに深く関わり、電磁気特性を左右するため、高度なノウハウとコントロール技術が必要となります。フェライトコアの製造工程と関連技術を下図に示します(フェライトコアの材料設計技術などについては、本シリーズVol.2をご参照ください)。
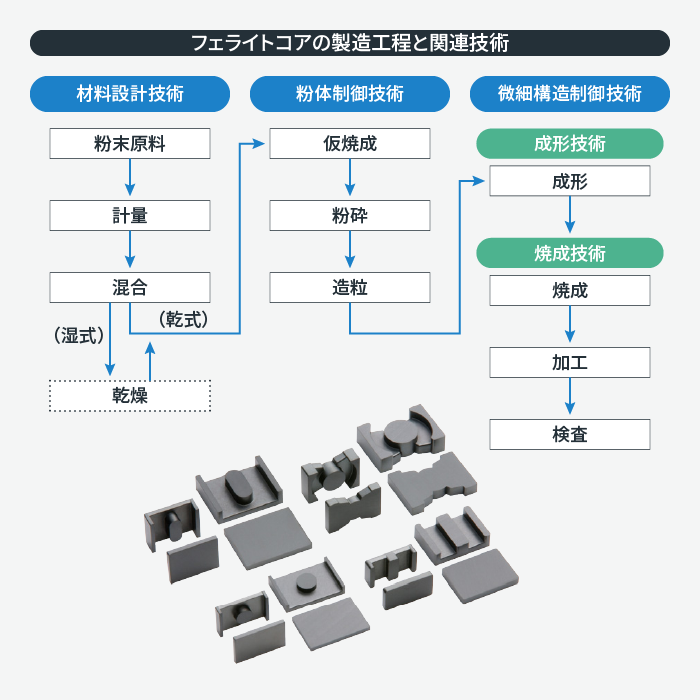
成形・焼成プロセスは、フェライトの微細構造や電磁気特性に深く関わる。
フェライトコアの成形技術とは
成形技術にはさまざまな種類がありますが、粉末を原料とするセラミックス製品においては、金型とプレス機による加圧成形法が主流です。
加圧成形法には原料を粉末のまま金型に入れてプレスする乾式と、原料を水と混ぜてスラリー状にしてから、金型に入れてプレスする湿式があります。まずはフェライトコアや汎用的なフェライトマグネットに採用されている乾式の加圧成形法について解説します。
粉体の流動性に関わる安息角
一般にセラミックス製品は、原料となる粉末が微細であるほど緻密な微細構造が形成されます。ところが、粉末が細かすぎると、流動性が悪くなって金型による成形が困難になります。原料粉末の粒径と成形しやすさは、相反する関係にあるのです。
たとえば、砂時計の砂はさらさらと下に落ちて、円錐形の小さな砂山をつくります。この砂山の斜面の角度は、砂粒の大きさなどにもよりますが、35°前後となります。これを安息角(あんそくかく)といいます。一般に、粉末の粒径が小さくなるほど安息角は大きくなる傾向があります。砂粒よりも細かい小麦粉などでは、安息角は50°以上になり、さらさらとした流動性を示しません。
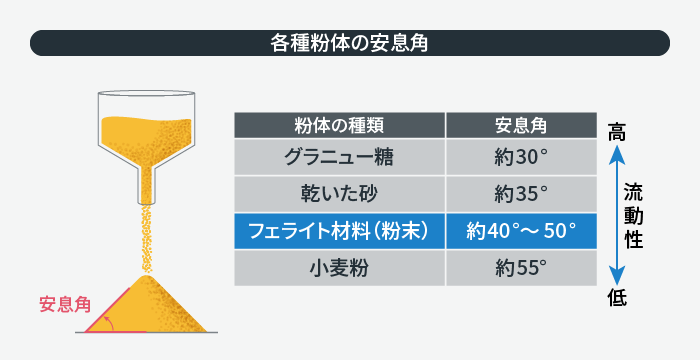
一般に安息角が大きいほど流動性は悪くなる。
粉末を顆粒にしてからプレス成形する理由
仮焼成で得られたフェライト材料は、緻密な微細構造を得るために、粒径が1μm程度の粉末になるように粉砕します。しかし、それでは流動性が悪く、きれいに成形できないので、粒径数10μm~100μm程度の顆粒にします。これを造粒といいます。粉末を顆粒とすることで適度な流動性が生まれ、金型のすみずみに行き渡るようになります。
主な造粒法として、スプレードライ(噴霧乾燥)法があります。粉砕した微粉末に水や適量のバインダ(結合材)などを加えてスラリー状にし、これを熱風に噴霧して瞬間的に乾燥させる方式です。バインダを加えるのは崩れにくい成形体とするためで、PVA(ポリビニルアルコール)などの有機化合物が使われます。
成形・焼成の前に行われる造粒はきわめて重要な工程ですが、加圧の仕方にもノウハウがあります。顆粒間のすきまの空気を逃がすために、また、成形体にクラックを生じさせないために、成形体や金型の動きを精密にコントロールする必要があります。
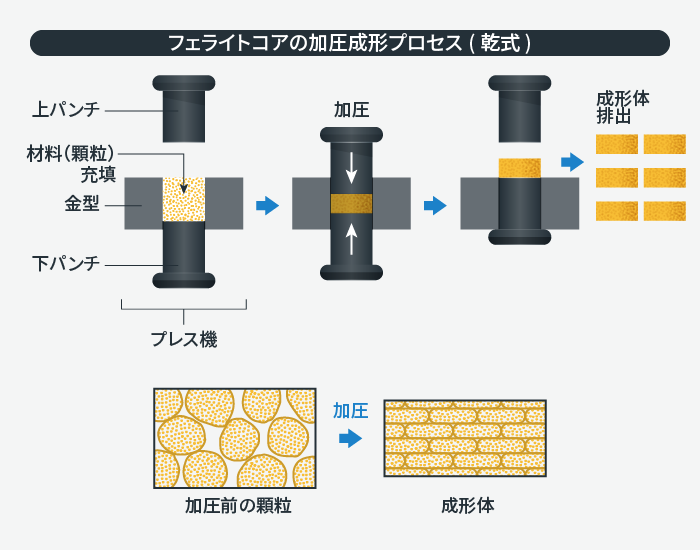
加圧・圧縮により顆粒間や顆粒内の空気は排出され、緻密な成形体となる。
フェライト生成は固体どうしの固相反応
成形体に残ったバインダ(結合材)は、焼成プロセスの初期段階で加熱により燃焼して排出されます。これを脱バインダ工程といいます。それから、徐々に温度を上げて、所定の温度に達したら一定温度を保って結晶粒を成長させ、その後、徐々に温度を下げていきます。この焼成工程は、およそ数時間~10数時間にわたります。
粉末原料は、まず仮焼成することでフェライト化し、焼成プロセス(本焼成)で、フェライト粒子は成長して緻密な多結晶体となります。
下図はMn-Zn(マンガン亜鉛)フェライトにおけるフェライト生成反応のモデルです。黒い球は主成分(酸化鉄)の原料粉末、赤い小さな球は微量添加物を表しています。温度の上昇とともに粉末原料や微量添加物が凝集し、化学反応によってフェライト結晶が生成されます。これは原料が溶融する温度以下で進行する固体どうしの反応であるため「固相反応」といいます。
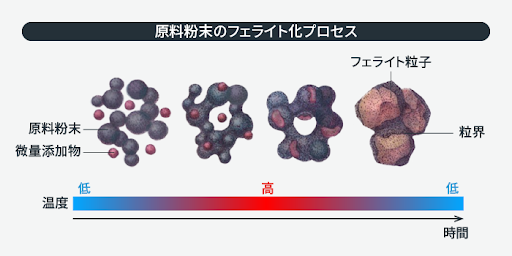
フェライト粒子の生成とともに、微量添加物は粒界に集まる。
フェライトの微細構造に関わる焼成温度と時間
結晶の生成とともに、微量添加物や気孔(ポア)などは、結晶粒の表面に集まって粒界を形成します。このプロセスがフェライト焼結反応の核心です。
一般に、焼成温度が高いほど結晶の粒は大きくなり、透磁率(磁束の通しやすさ)も高くなります。また、結晶粒の成長速度がゆるやかなほど、粒界層は厚くなり、電気抵抗が大きくなります。このように温度・時間・雰囲気(焼成炉内の気体成分)などの焼成条件によって、微細構造や特性が変化するため、高度なコントロール技術が必要になります。
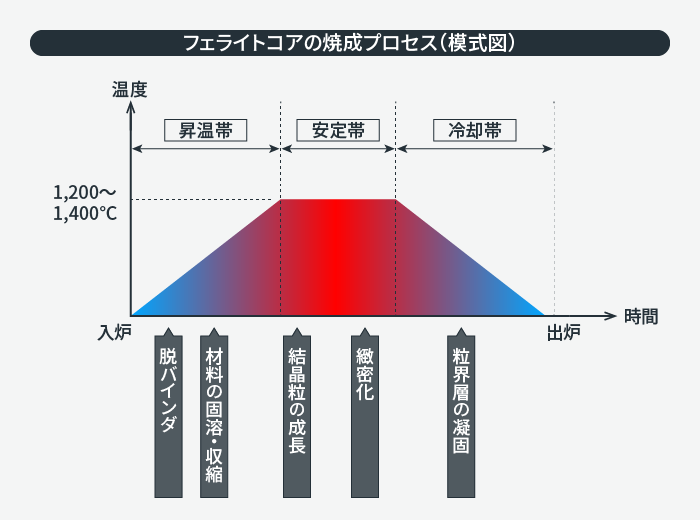
一般に焼成工程は数時間~10数時間に及ぶ。
高性能フェライトマグネットの成形技術とは
フェライトマグネットもフェライトコアと同じようなプロセス技術で製造されますが、成形法の違いにより、等方性磁石と異方性磁石に大別されます。等方性磁石は原料粉末を金型に入れて、そのままプレス成形する最も簡単な方式。一方、異方性磁石は外部磁界を加えながら成形する方式(磁界中プレス成形)が採用されます。
フェライトマグネットの結晶(マグネトプランバイト型)は、下図のような六方晶の結晶体(薄い六角柱のような形状)で、その中心軸方向が磁化されやすい性質をもっています(磁化容易軸という)。等方性磁石は原料粉末を金型に入れ、そのままプレスして成形する最も簡単な方式で作られ、磁化容易軸の方向はバラバラです。そこで、外部から磁界を加えながら成形すると、磁界方向に結晶軸がそろいます。これを異方性磁石といい、等方性磁石よりも強力な磁石となります。
また、原料粉末に水を混ぜてスラリー化して磁界の中で圧縮成形すると、粉末どうしの摩擦が減って、より緻密に整列します(湿式磁界中成形)。
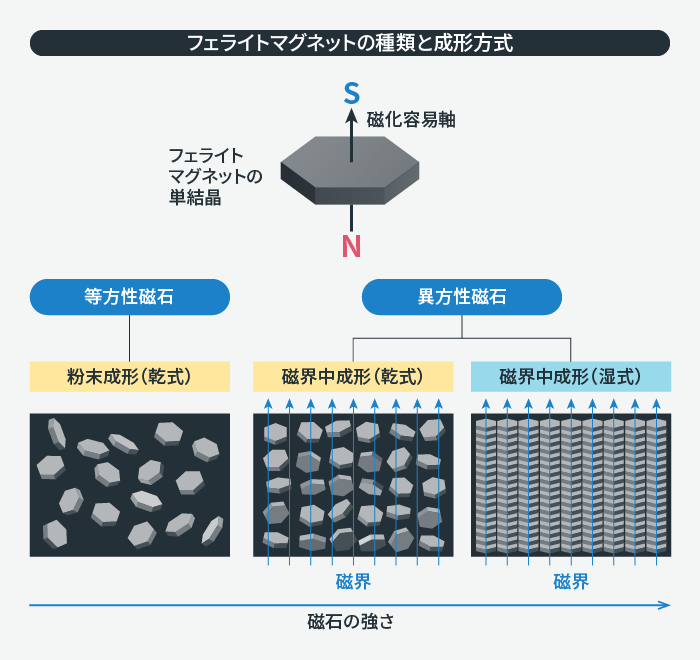
等方性のフェライトマグネットは、磁力では異方性タイプに劣るが、低コストで量産でき、どの方向にも自由に着磁できるのが利点。
車載DCモータなどに使われる異方性フェライトマグネットの製造には、主に湿式磁界中成形方式が採用されています(下図)。この方式は、成形の過程で圧縮加圧・脱水工程が加わるため、時間やコストがかかりますが、他の成形方式とくらべてハイパワーなフェライトマグネットを作ることができます。
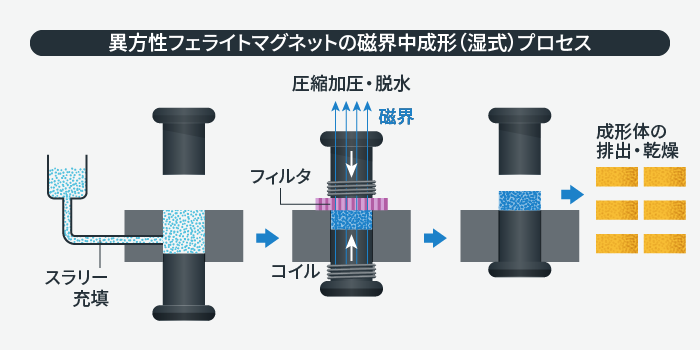
ハイパワーの高性能フェライトマグネットは、湿式磁界中成形タイプである。
フェライトマグネットの薄肉化を実現したTDK
フェライトマグネットは、セラミックスであるため欠けやすく、薄く作ることが困難です。用途によっては焼成した後に切削加工して薄肉化したりしますが、コストアップは避けられません。
この問題を解決したのがTDKのNS1工法です。世界トップクラスの磁石特性をもつフェライトマグネット材FB12シリーズ(ハイパワーLa-Co系)をベースにした新材質と独自の高密度充填技術により、厚さ2mm以下という驚異的な薄肉化を実現しました。FB13B材として提供され、車載DCモータの小型・高性能化などに大きく貢献しています。
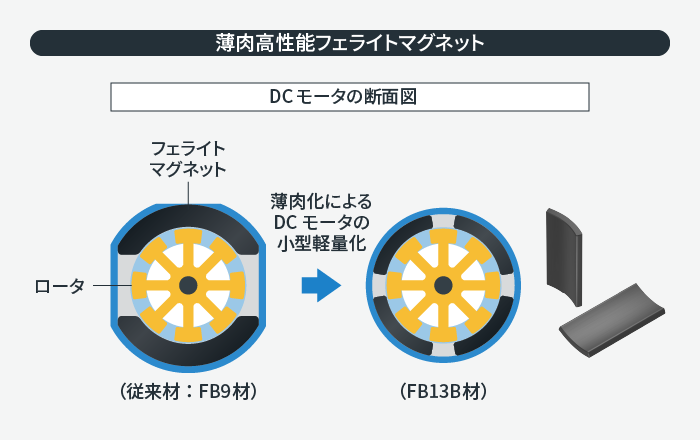
ここまで、磁性体セラミックスである「フェライトコア」や「フェライトマグネット」を中心に成形技術・焼成技術を解説してきました。このような成形・焼成技術は、コンデンサの材料となる誘電体セラミックスや、圧電デバイスの材料となる圧電体セラミックス、また、サーミスタやバリスタの材料となる半導体セラミックスなど、あらゆるエレクトロセラミックス製品の特性や品質にも関わる重要なプロセス技術です。多結晶体ならではの多彩なエレクトロセラミックスのパフォーマンスは、粉体制御技術や微細構造制御技術などを駆使した成形・焼成プロセスにおいて生まれます。成形技術や焼成技術が、きわめて重要なTDKのコアテクノロジーになっていることが、おわかりいただけるでしょう。
独自の製造設備による生産技術も、TDKのコアテクノロジーの一つです。TDKでは成形から焼成までのフェライトコアの全工程をコンパクトに集約した先進の自動化ライン(DSS:Direct Sintering System)を開発するなど、さらなる効率化と品質向上にも努めています。
TDKは磁性技術で世界をリードする総合電子部品メーカーです