TDKのコアテクノロジー
Vol.4
積層セラミックチップコンデンサ(MLCC) と「微細構造制御技術」
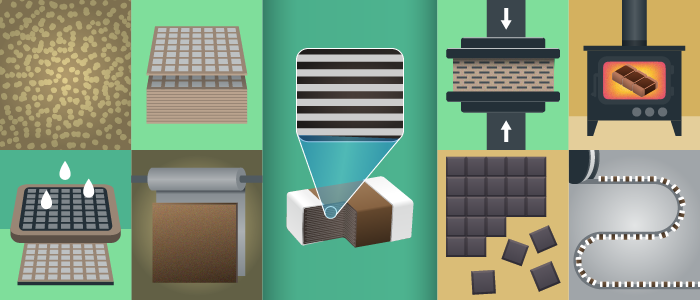
抵抗、コイル(インダクタ)とともに3大受動部品のひとつであるコンデンサの主流は、チップタイプの積層セラミックチップコンデンサ(MLCC)です。数量・規模で全コンデンサ生産量の90%超を占めていて、スマートフォンには500個前後、ノートパソコンには1,000個前後も使用されているように、電子機器はもとより電装化が進む自動車においても不可欠な電子部品です。MLCCの製造には、使用される誘電体セラミックスの材料組成とともに、焼成工程における高度な「微細構造制御技術」が求められます。まずはセラミックコンデンサのルーツと歴史をたどってみましょう。
磁器がチャイナと呼ばれるのは?
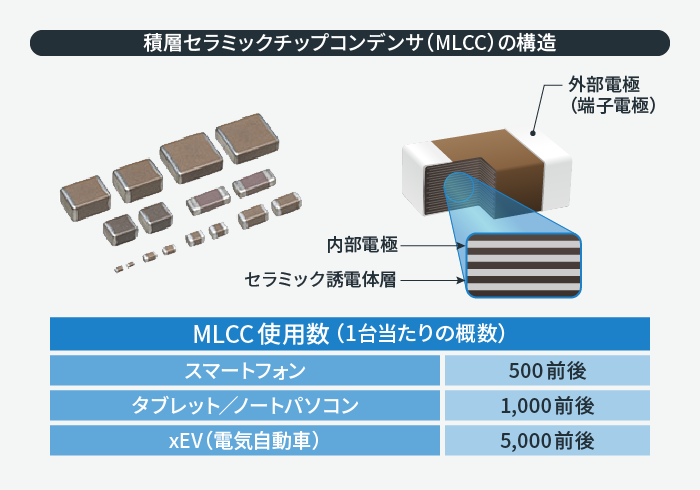
MLCCとはMulti-Layer Ceramic Capacitorの略語。英語圏ではコンデンサはキャパシタと呼ばれる。
陶器や磁器などの窯業(ようぎょう)製品は、一般に「セラミックス」と呼ばれますが、これはギリシャ語で焼き物を意味する「ケラモス」が語源です。このうち磁器のことを特にチャイナ(china)と呼びますが、ルネサンス期のヨーロッパで、中国(China)製の白磁が熱狂的なブームを巻き起こしたことに由来します。
古くからの青磁の製法を発展させて、中国で初期の白磁が作られたのは6世紀頃といわれ、10世紀頃の北宋の時代には芸術性の高い白磁が製造されるようになりました。さらに元や明の時代になると、白磁に染付(そめつけ)や色絵付(いろえつけ)による模様をほどこした華麗な製品が量産され、ヨーロッパ向けにさかんに輸出されました。なかでも中国江西省の景徳鎮(けいとくちん)の製品は世界的に有名です。
ファインセラミックスの先駆製品
磁器がそれまでの土器や陶器と一線を画すのは、その原料の違いにあります。
土器や陶器の素地が赤色や褐色なのは、原料の粘土に鉄分などの不純物が多く含まれるためです。一方、磁器はカオリナイト(カオリン石)と呼ばれる鉄分などの少ない特殊な白色粘土に、ケイ石(石英)や長石の粉を配合したものを原料とし、約1,200~1,500℃の高温で焼成されます。カオリナイトだけで成型して焼いても、熱によって崩れてしまいますが、石英が骨格となり、溶けた長石がガラス質となって焼結することで、硬質で半透明の白磁となるのです。カオリナイトという名は、良質な白色粘土の産地である景徳鎮近くの高陵(カオリン)に由来します。
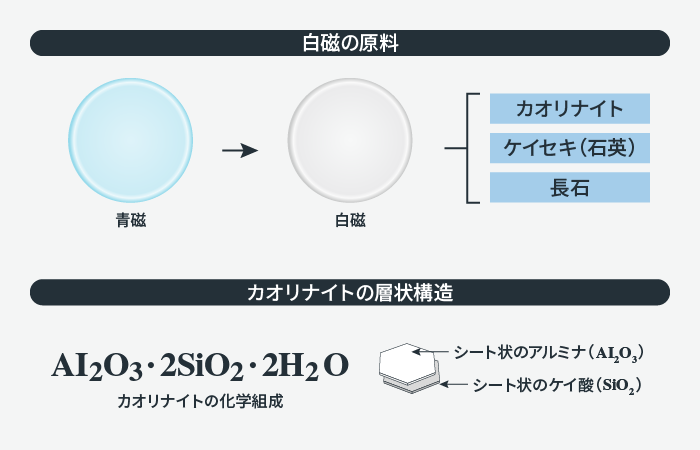
青磁は鉄分を含む粘土や釉薬(ゆうやく)により淡い青色となる。白磁は鉄分の少ない特殊な白色粘土と透明釉薬を用いる。カオリナイトは層状構造をもち、シート間の水分子により、シートどうしは滑りやすくなって粘土特有の塑性を示す。
カオリナイトは産地がかぎられるうえ、原料の調合や製法が長らく秘密とされたため、日本で製造されるようになったのは17世紀の有田焼から、ヨーロッパでは18世紀ドイツのマイセン磁器が始まりです。
原料の純度や割合、焼成の温度や時間などを精密に制御することで得られる窯業製品は、ファインセラミックスと呼ばれます。窯業に歴史的イノベーションをもたらした白磁は、ファインセラミックスの先駆けともいうべき製品でした 。
多種多様なエレクトロセラミックス
ファインセラミックスには、工具やナイフ、自動車エンジン部品など、機械的機能を利用したもの(構造用セラミックス)、人工骨や人工歯根など、生体適合機能を利用したもの(生体材料用セラミックス)のほかに、セラミックスならではの電気的・磁気的機能を電子材料として利用したものがあり、これをエレクトロセラミックス(電子セラミックス)といいます。
エレクトロセラミックスには、次のような種類があり、それぞれの特性を生かして、さまざまな電子部品に応用されています。
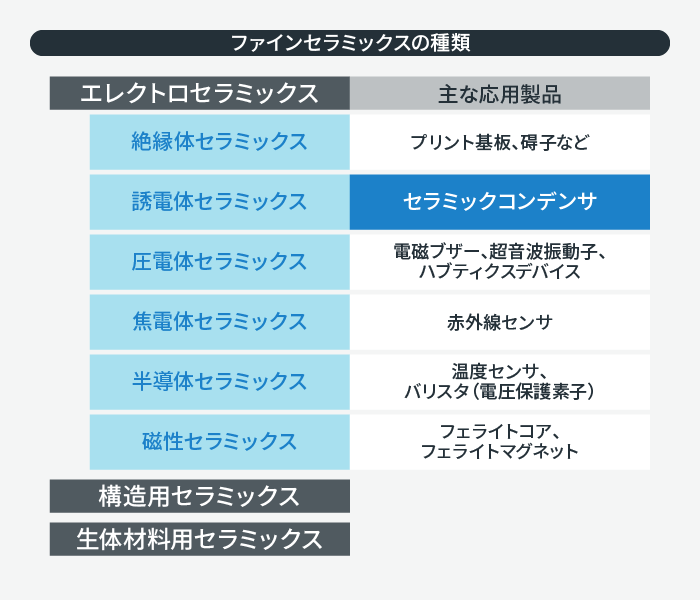
コンデンサの基本構造と誘電体の役割
本記事のテーマである積層セラミックチップコンデンサ(MLCC)に用いられるエレクトロセラミックスは、誘電体セラミックスというタイプです。誘電体とは、電界を加えるとプラスとマイナスに電気分極(誘電分極)する物質のことです。誘電体は直流電流を流さないことから、絶縁体(あるいは不導体)とも呼ばれます。言い換えれば、直流電流を通さない絶縁体が、電気分極して電荷(電気エネルギー)を蓄える性質を利用したのがコンデンサです。
もともとコンデンサは、18世紀イタリアのボルタが摩擦電気を蓄える装置として考案し、これをコンデンサトーレ(凝縮器という意味)と呼んだことに由来します。
下図のように、空間を隔てて対向する2枚の電極にリード線を設けたのがコンデンサの基本構造です。コンデンサが蓄えられる電荷の量すなわち静電容量は、電極の面積に比例し、電極間の距離に反比例します。また、電極間に誘電体をはさむと、誘電体の誘電率(電気分極の起こりやすさ)に比例して静電容量は大きくなります。
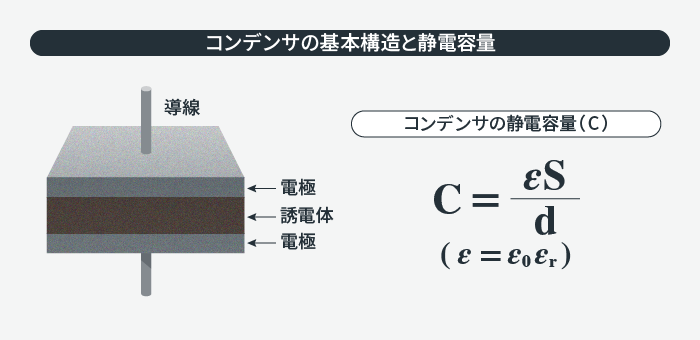
C:コンデンサの静電容量[F] S:電極面積[m2] d:電極間距離[m] ε:誘電体の誘電率[F/m]
ε0:真空の誘電率(8.855×10-12) [F/m] εr:誘電体の比誘電率(真空の誘電率に対する比)
チタン酸バリウムは驚異的な誘電体セラミックス
セラミックスを誘電体として用いたコンデンサは、セラミックコンデンサと呼ばれます。
初のセラミックコンデンサは、19世紀末に発明されたステアタイト磁器コンデンサです。これは滑石(タルク)を原料とするステアタイト(ケイ酸マグネシウム:MgSiO3)を誘電体として用いたもので、1920-30年代になると酸化チタン(TiO2)を誘電体とするセラミックコンデンサも発明されました。
比誘電率は誘電体の種類によって大きく異なり、空気は約1、ゴム、ガラス、イオウ、ステアタイトなどは10前後ですが、 酸化チタンは100前後もあり、高周波特性にすぐれるため、初期の無線通信機器などに多用されました。
セラミックコンデンサに驚異的な飛躍をもたらしたのは、1940~42年頃、アメリカ、ソ連、日本でほぼ同時に発見されたチタン酸バリウム(BaTiO3:略称、チタバリ)です。その比誘電率は約1,000~20,000にも及ぶため、セラミックコンデンサの大容量化に大きく貢献し、1960年代にはチップタイプの積層セラミックチップコンデンサ(MLCC)も開発されました。なお、MLCCには温度特性にすぐれる低誘電率タイプと、大容量を特長とするチタン酸バリウム系の高誘電率タイプがありますが、本記事では高誘電率タイプを中心に解説します。
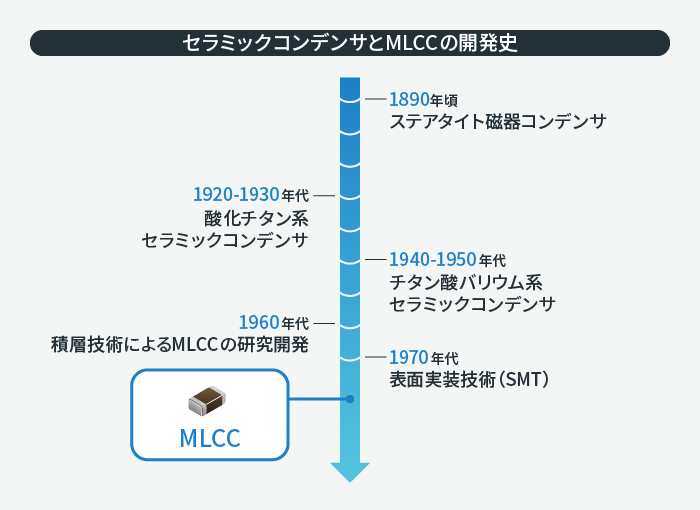
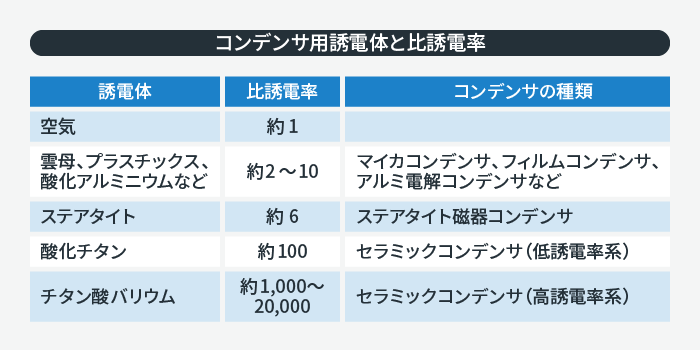
真空の誘電率に対する誘電体の誘電率を比誘電率という。
暴れ馬のようなチタン酸バリウムを調教する素材技術
チタン酸バリウムは外部電界がなくても室温で電気分極(自発分極という)している物質で、この性質は一般的な誘電体(常誘電体)に対して強誘電体といいます。
強誘電体は温度上昇とともに常誘電体へと変化(相転移)します。この温度をキュリー温度(キュリー点)といいます。
チタン酸バリウムは驚異的に高い誘電率をもちながら、きわめて癖のある誘電体セラミックスです。キュリー温度は約130℃で、この温度をピークとして高い誘電率を示しますが、この温度帯は室温を超えるので実用に不向きです。そこで、添加物によってキュリー温度を下げます。この添加物をシフターといいます。また、添加物により誘電率の鋭いピークをなだらかにし、室温域の広い温度範囲で使用できるようにします。この添加物をディプレッサといいます。
野生の暴れ馬のように、きわめて癖のあるチタン酸バリウムを、添加物でたくみに調教することにより、セラミックコンデンサへの利用が可能になったのです。こうして実用化されたのが、チタン酸バリウムを主成分とする高誘電率系のセラミックコンデンサです。
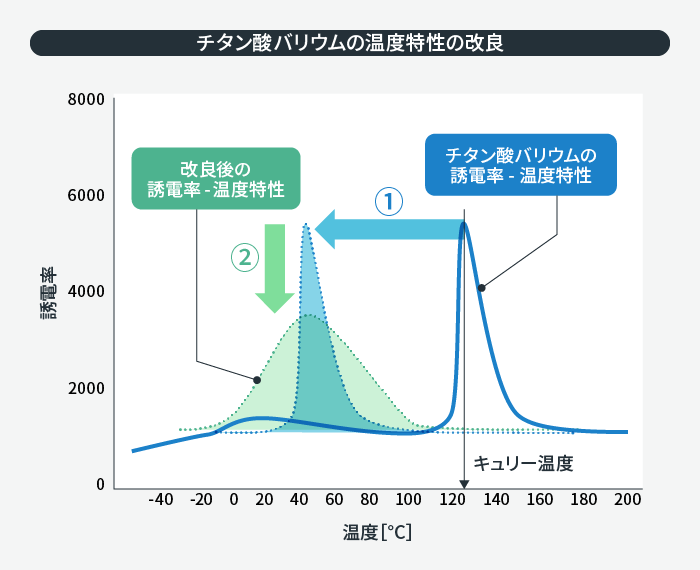
①微量添加物(シフター)によりキュリー温度を下げて、ピークを室温域に移動する。
②微量添加物(ディブレッサ)により急峻なピークをなだらかにする。
結果として、室温域で高い誘電率を確保・利用できる。
誘電体セラミックスの微細粉の製法とシート工法
積層工法によるMLCCの製法はシート工法が主流です。まず誘電体セラミックスの微細粉を溶剤や分散剤、バインダ(結合剤)などと混合して泥状のスラリーとし、これをキャリアフィルム上に薄く伸ばして誘電体のグリーンシート(生のシート)を形成します。
次にこのグリーンシートに内部電極パターンをスクリーン印刷したものを積み重ねて圧着してから、多数のチップ個片に切断し、これを焼成炉でセラミックス化してから、外部電極をめっきしてMLCCが製造されます。
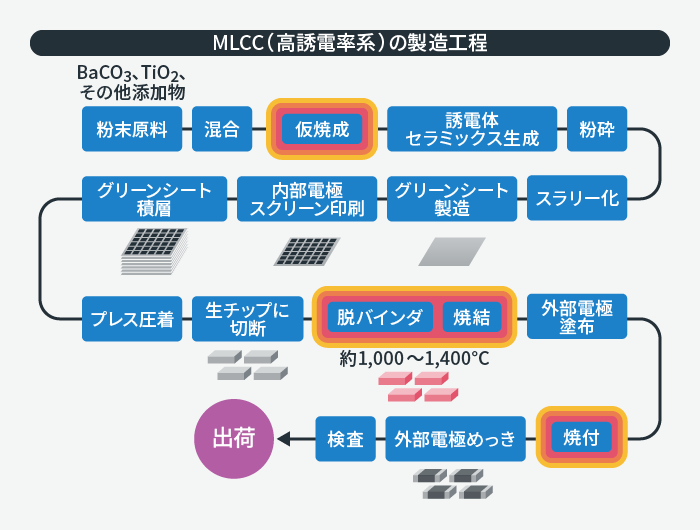
MLCCの大容量化・小型化をもたらした「微細構造制御技術」
前述したように、コンデンサの静電容量は、電極間の距離が短く、電極の面積が広いほど大きくなるため、MLCCの大容量化を図るためには、セラミックスシートの薄層化と多層化が技術目標となります。
MLCCに用いられるチタン酸バリウム系の誘電体セラミック材料は、化学合成された高純度の酸化チタン、炭酸バリウム、および微量添加物の粉末を混合して原料とします。
シート形成されるMLCCの誘電体層は、石垣上に積み重なった複数の誘電セラミック粒子で構成されます。誘電体層を薄層化するには、誘電体セラミック粒子が微細かつ均一(粒度分布が良好)であることが求められます。
また、MLCCを構成するチタン酸バリウム系の誘電体セラミック粒子は、高誘電率の結晶からなるコア部と、それを取り囲む比較的誘電率の低いシェル部の2相構造となっています。これをコアシェル構造といいます。添加物はシェル部に偏析(成分が不均一に偏在すること)して特性に影響を与えることが知られていて、焼成条件や微量添加物の配合の最適化などにより、特性を改善することができます。たとえば、ジスプロシウム(Dy)やホルミウム(Ho)などの希土類元素を添加物として加えてシェル部に固溶させることで、誘電率の温度依存性(温度上昇とともに誘電率が低下すること)を小さくしたり、寿命を延長できたりします。このように、MLCCの薄層化・大容量化には、コアシェル構造を含めた高度な微細構造制御技術が求められます。
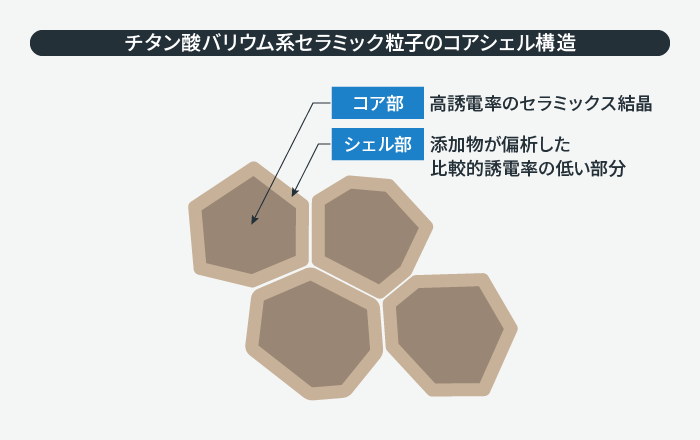
焼成条件や添加物によって粒径や特性などを制御できる。たとえば、ジスプロシウム(Dy)やホルミウム(Ho)などの希土類元素を添加してシェル部に固溶させることで、誘電率の温度依存性や寿命などが改善される。
1μm以下の薄層化、1,000層以上の多層化を実現
材料設計技術や微細構造制御技術などを駆使した薄層化・多層化に進展により、1980年以降、MLCCは同サイズ比較で1,000倍以上の大容量化を達成。2010年代には、1層の層間厚みは1ミクロン以下、層数1,000以上にも及ぶ多層化技術を確立して製品化されました。
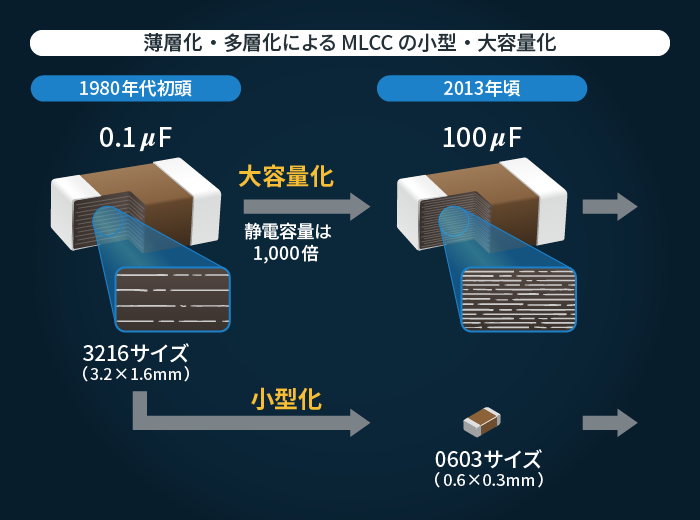
極小化限界・大容量限界を超えるソリューション
MLCCの小型・大容量化には、誘電体セラミックス粒子が微細かつ粒度分布が良好であることが必須条件ですが、微細であればあるほどよいというわけではありません。誘電率は粒径100nm前後をピークとして、それより微細化すると低下していくからです。これは「サイズ効果」と呼ばれます。
この問題をブレイクスルーするため、50nm以下のナノ粒子でも高い誘電率をもつ新素材の研究開発が進められています。また、0201サイズ(0.2×0.1mm)よりも小さなMLCCの量産技術も確立されていますが、あまりに小さくなるとマウンタ(自動実装機)によるプリント基板への実装が困難になります。このため、多数のチップ部品を二次元配列する従来の表面実装技術(SMT)とともに、MLCCやインダクタ、ICなどを三次元的に集積して小型化を図るモジュール化技術の高度化も進められています。
さらに、近年需要が伸びている車載用途のMLCCにおいては、小型化のニーズよりも、酷寒から灼熱まで広い使用温度範囲において、より安定した特性をもつ高信頼性の製品が求められています。
MLCCは電子機器で最も多用されるチップ部品。20世紀半ば以降発展してきた薄層化・多層化による小型化・大容量化のトレンドは、技術的困難を克服しながら今後もなお続いていくことでしょう。そして、5G通信機器、ウェアラブルデバイス、ロボティクス、xEV(電気自動車)や自動運転車など、新たな市場においてますます需要が増えていくことは間違いありません。TDKでは一般グレード、車載グレード、高信頼グレードの各種仕様のMLCCを豊富にラインアップに、全世界の先進市場ニーズに応えています。
TDKは磁性技術で世界をリードする総合電子部品メーカーです