The Wonders of Electromagnetism
The History of Refrigerators and the Evolution of Refrigeration Technology
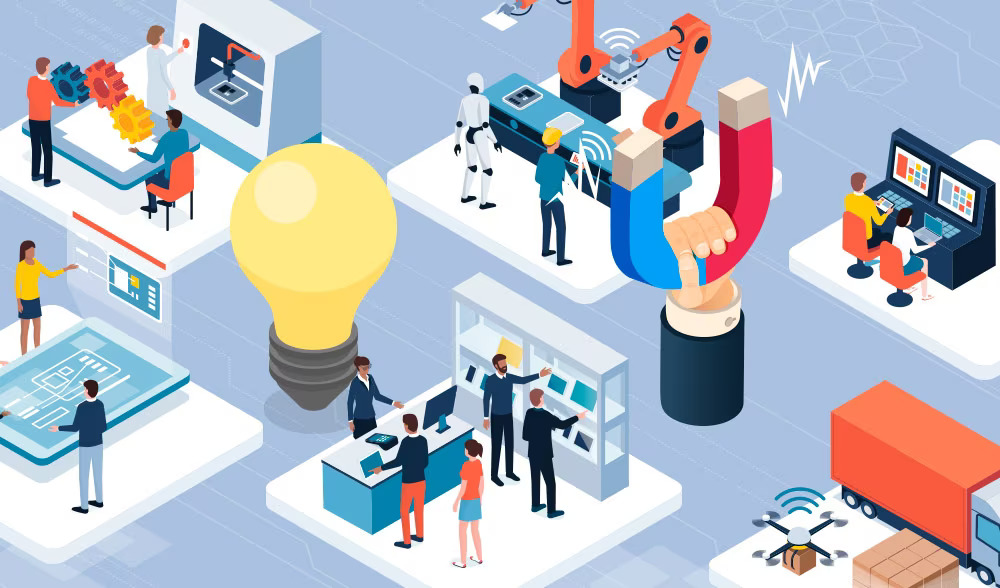
Refrigerators are continually increasing in size. For example, the share of refrigerators classified as “large” (401 liters or more in capacity) among domestic shipments in Japan grew from 33% in 2002 to 46% in 2022. Large refrigerators—particularly those with ample freezer space—have become popular for storing food purchased in bulk, dishes cooked in volume for preservation, and home-delivered items. Since the onset of COVID-19, more households are purchasing a second freezer. Throughout history, humans have devised a variety of methods to keep food cold.
How did people obtain ice before electricity was available?
At the foothills of Mount Fuji, lava caves known as fu-ketsu and hyo-ketsu (meaning “wind pit” and “ice pit,” respectively) have long been tourist attractions. Because they were cool and refreshing even in summertime, they were utilized as storage chambers for ice during Japan’s Edo period. Natural ice preserved in these enclaves was transported all the way to Edo Castle to be offered to the shogun, the feudal ruler of the country at the time.
The technological challenge of producing artificial ice began in early modern Europe. Sprinkling water on the ground has a cooling effect because the water absorbs heat from the ground as it evaporates (heat of vaporization). When the internal pressure of a container with some water inside is reduced using an air pump, the water becomes more prone to evaporation and eventually cools down to sub-zero temperatures. Although experimental, ice was successfully produced in the 18th century using this method.
The roots of electric refrigerators can be traced back to the mechanical ice machine conceived by American inventor Jacob Perkins in 1834. It utilized a volatile liquid, such as ether, as a refrigerant. A hand-driven air pump lowered the pressure, which forced the refrigerant to evaporate, removing heat from the surroundings and creating a cooling effect. The vaporized refrigerant was repressurized by the pump and sent to a cooling coil, where it was liquefied and returned to the evaporator. This mechanism, known as vapor compression refrigeration, remains essentially unchanged in today’s refrigerators.
Ice machines using ammonia as a refrigerant arrived in Japan in the early Meiji period. When Yukichi Fukuzawa fell ill with a fever in the summer of 1870, a professor at Daigaku Toko (a predecessor institution of The University of Tokyo) mastered the machine’s operation and trained students at Keio University, who used it to create ice for fever relief purposes. This marked the beginning of artificial ice production in Japan.
By the middle of the Meiji period, ice factories had been built throughout the country, making ice available even during the summer. Before the proliferation of electric refrigerators, appliances known as iceboxes were commonly used. They resembled wooden coolers with one door on the top and another on the bottom. With a large block of ice placed on the upper shelf, the cooled air would descend, effectively chilling beverages like soda or beer stored inside.
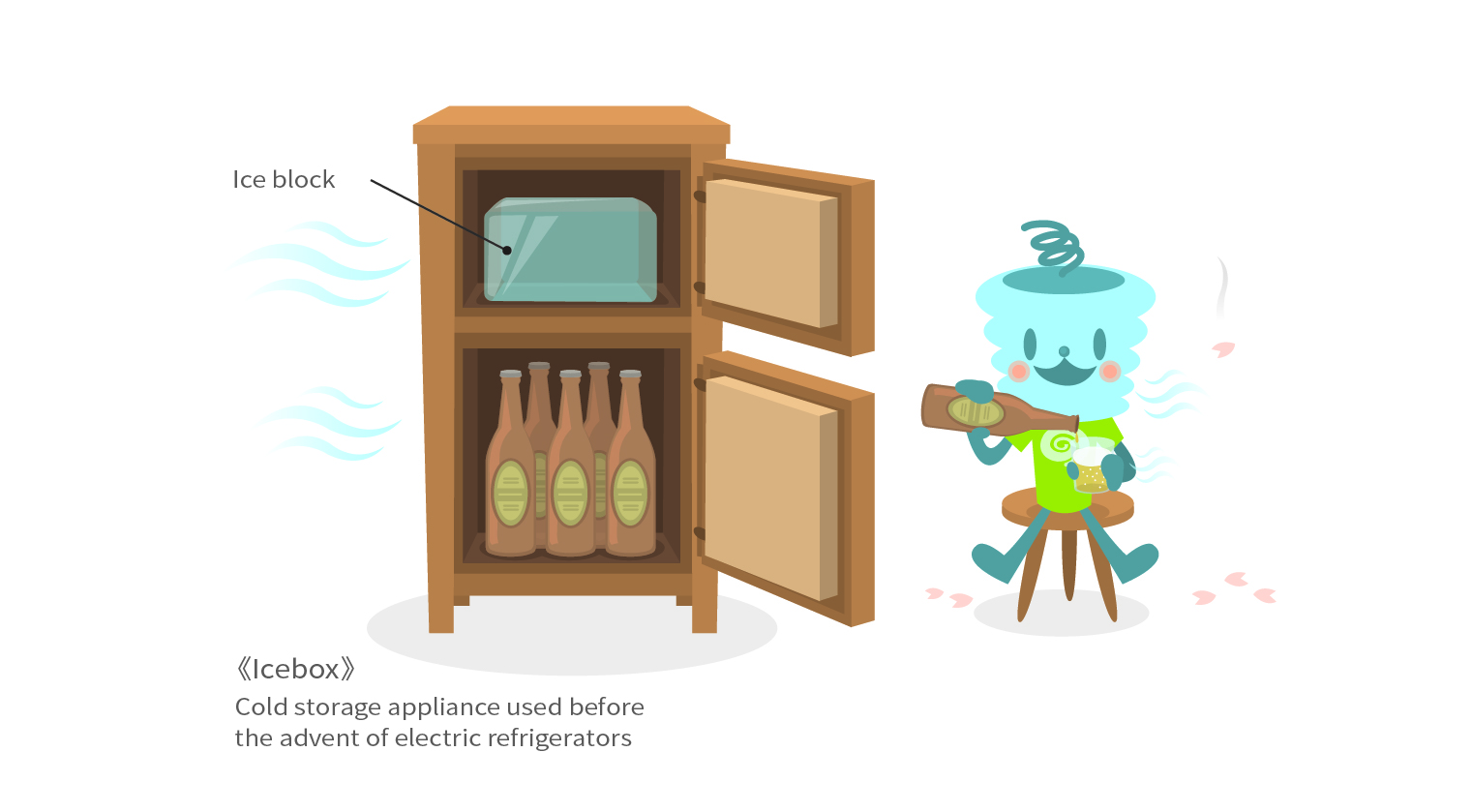
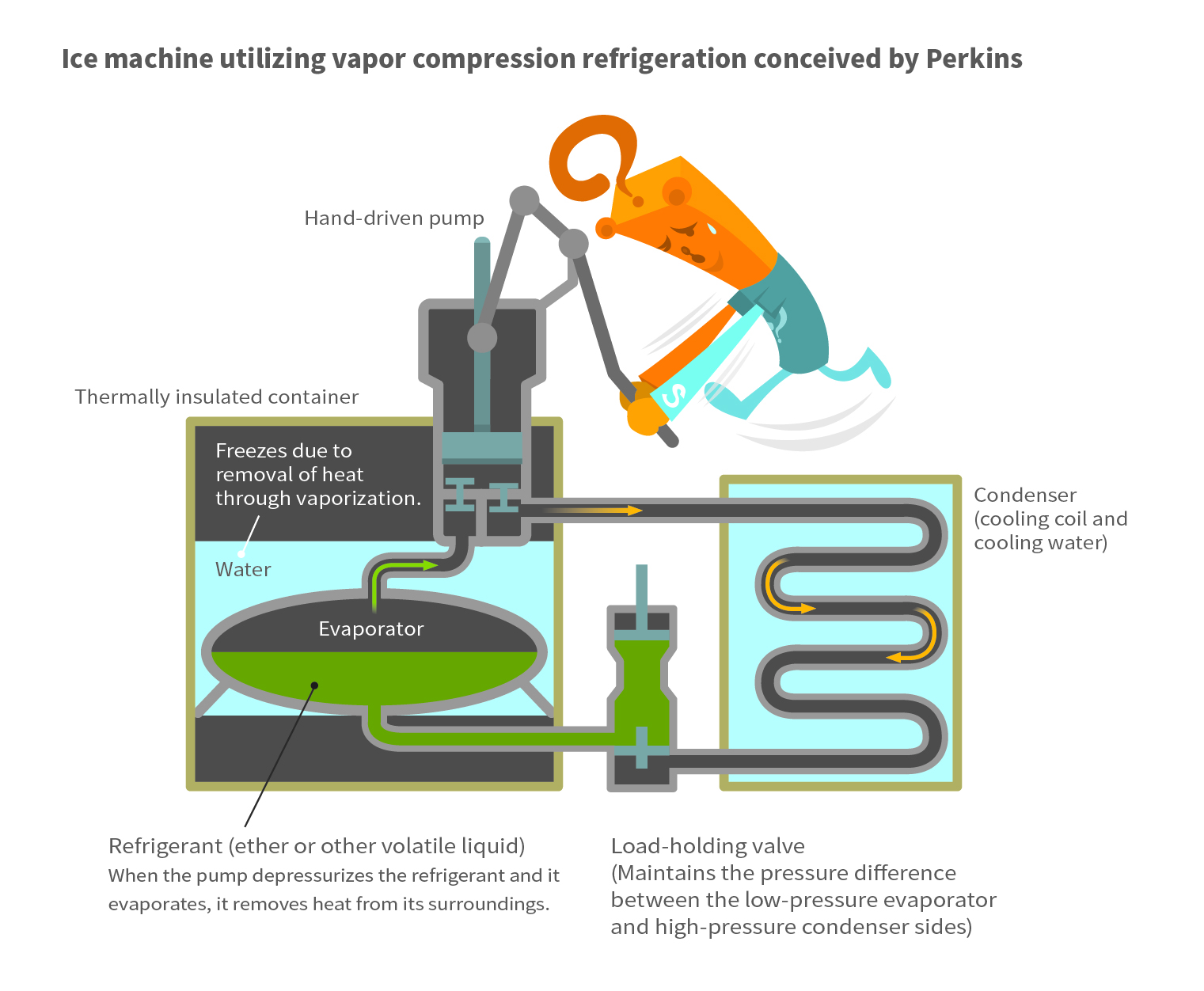
Electric refrigerators use compressors and inverters to lower temperatures
In electric refrigerators, the refrigerant is pressurized and depressurized by electrical power instead of manual work. The characteristic humming noise of a refrigerator is emitted by its motor-driven compressor. The compressor’s role is to compress the refrigerant gas. The gas, heated and pressurized by the compressor, is sent to a winding pipe known as a condenser, where it releases heat as it liquefies. This is why heat is emitted from the rear of a refrigerator. The liquefied, lower-temperature refrigerant is sent through a narrow pipe called a capillary tube to the evaporator located inside the refrigerator’s main compartment. Here, the sudden drop in pressure forces the refrigerant to vaporize, which absorbs heat and cools the surroundings. The refrigerant, now a gas, is returned to the compressor, completing the cycle. In short, the refrigerant cools the refrigerator’s interior by repeating the process of liquefaction and vaporization. This is referred to as the refrigeration cycle.
In the past, chlorofluorocarbons (CFCs) were used as the refrigerant in refrigerators. However, due to their role in the depletion of Earth’s ozone layer, they were later replaced by CFC substitutes. Today, because most CFC substitutes have a significant greenhouse effect, hydrocarbons like isobutane and cyclopentane are used instead.
Refrigerators account for a substantial portion of household energy consumption, second only to air conditioners. Unlike air conditioners, refrigerators run around the clock, which drove the development of numerous energy-saving measures over the years. Among them, a groundbreaking innovation emerged in the 1990s: inverter technology refrigerators.
The rotational speed of a compressor motor is linked to the frequency of the power supply’s alternating current (usually 50 or 60 Hz). Consequently, conventional compressors could only run at a constant speed and power. However, with inverter technology, the alternating current is first converted to direct current, then reconverted into alternating current at a variable frequency (or variable voltage), which enables the compressor motor’s speed to be controlled freely.
For instance, during the winter, the compressor’s speed can be reduced to prevent overcooling. Or, when the door is opened and the interior temperature rises, the compressor can be run momentarily at high power to quickly bring the temperature back down before returning it to its previous speed. Data from temperature sensors and other information enable these fine power adjustments, enhancing energy efficiency. In addition to temperature sensors, a wide variety of TDK products are utilized in refrigerators, including inverter circuits for adjusting the speed of compressor motors, the motors themselves, and microcontrollers and power supplies for controlling their operation.
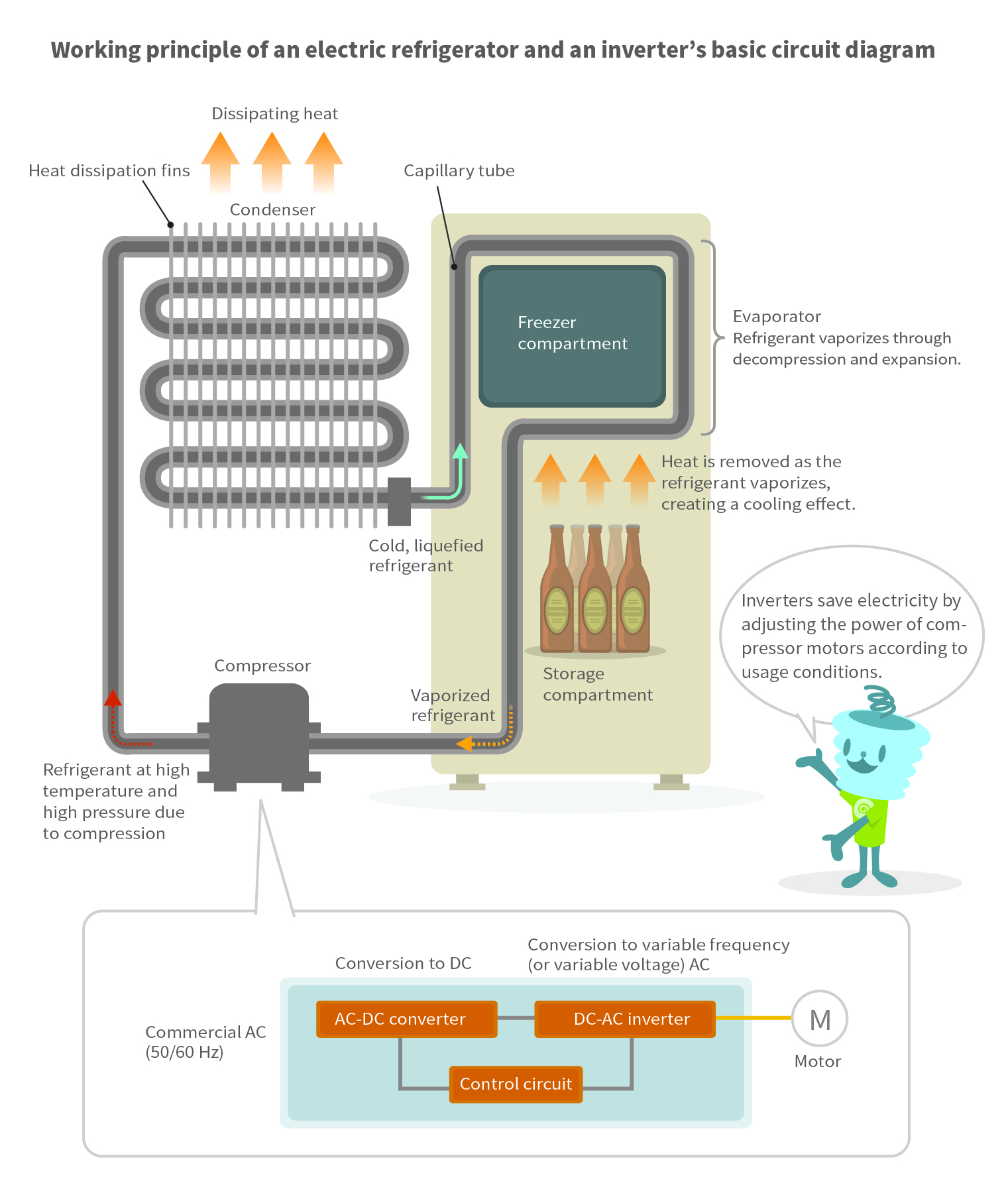
Natural gas refrigeration: Why a frozen food factory sits next to an LNG terminal
Today, almost 30% of Japan’s electricity is generated from thermal power generation fueled by liquefied natural gas (LNG), which is primarily methane. The utilization process of LNG bears resemblance to the refrigeration cycle of a refrigerator. First, the natural gas is cooled and compressed into liquid form at the source located abroad, similar to the role of a refrigerator’s compressor. The liquefied LNG is transported on tankers, then regasified at domestic LNG terminals for use as fuel. The regasification process absorbs heat from its surroundings, much like a refrigerator’s evaporator. This is referred to as cold energy. Given the vast amount of cold energy involved, releasing it into the environment would be terribly wasteful. This explains why many manufacturing plants, such as those producing liquid nitrogen, liquid oxygen, dry ice, frozen foods, etc., are adjacent to LNG terminals: they utilize the cold energy released during the regasification of LNG.
There is a different type of refrigerator that can be called an “electronic” refrigerator since it operates without refrigerants or motors. It utilizes a phenomenon known as the Peltier effect. When a P-type and N-type semiconductor are joined together and an electric current is passed through them, one side generates heat while the other exhibits cooling. Although its power is limited, the simplicity of the mechanism and the lack of motor noise make it suitable for use in small refrigerators for hotel and hospital rooms. (See this article for a more detailed explanation of how refrigerators based on the Peltier effect work.)
Cooling liquid helium to extremely low temperatures is accomplished by a technique known as magnetic refrigeration, which leverages magnetic materials. Magnetic materials are substances that become magnetized when subjected to magnetic fields from the outside. Their magnetic properties change depending on the collective behavior of their micromagnetic particles, determined by the rotation (more technically, the spin) of electrons within the substance. In the absence of a magnetic field, the spins inside a magnetic material are in a disordered state and randomly oriented. When an external magnetic field is applied, the spins align with the direction of the magnetic field. When the magnetic field is removed, the spins return to the disordered state—but as that occurs, heat is absorbed from the surroundings. This phenomenon is known as adiabatic demagnetization. Although the heat removed each time is minimal, repeating the process achieves cooling to extremely low temperatures.
In recent years, the development of magnetic materials capable of adiabatic demagnetization at “high” temperatures (i.e., close to room temperature) and powerful magnets capable of generating intense magnetic fields have sparked research into applying magnetic refrigeration to refrigerators. If successfully commercialized, this technology can become the most significant breakthrough in energy conservation in refrigeration since inverters.
To reach ultra-low temperatures close to absolute zero (0 K, or -273 °C), a technique called nuclear adiabatic demagnetization is additionally applied. While the magnetism of a substance is primarily attributable to the spin and orbital motion of electrons, the magnetic moments of the atomic nucleus are also partially involved. By using a powerful external magnetic field to align the orientations of nuclear magnetic moments, temperatures approaching absolute zero are achievable.
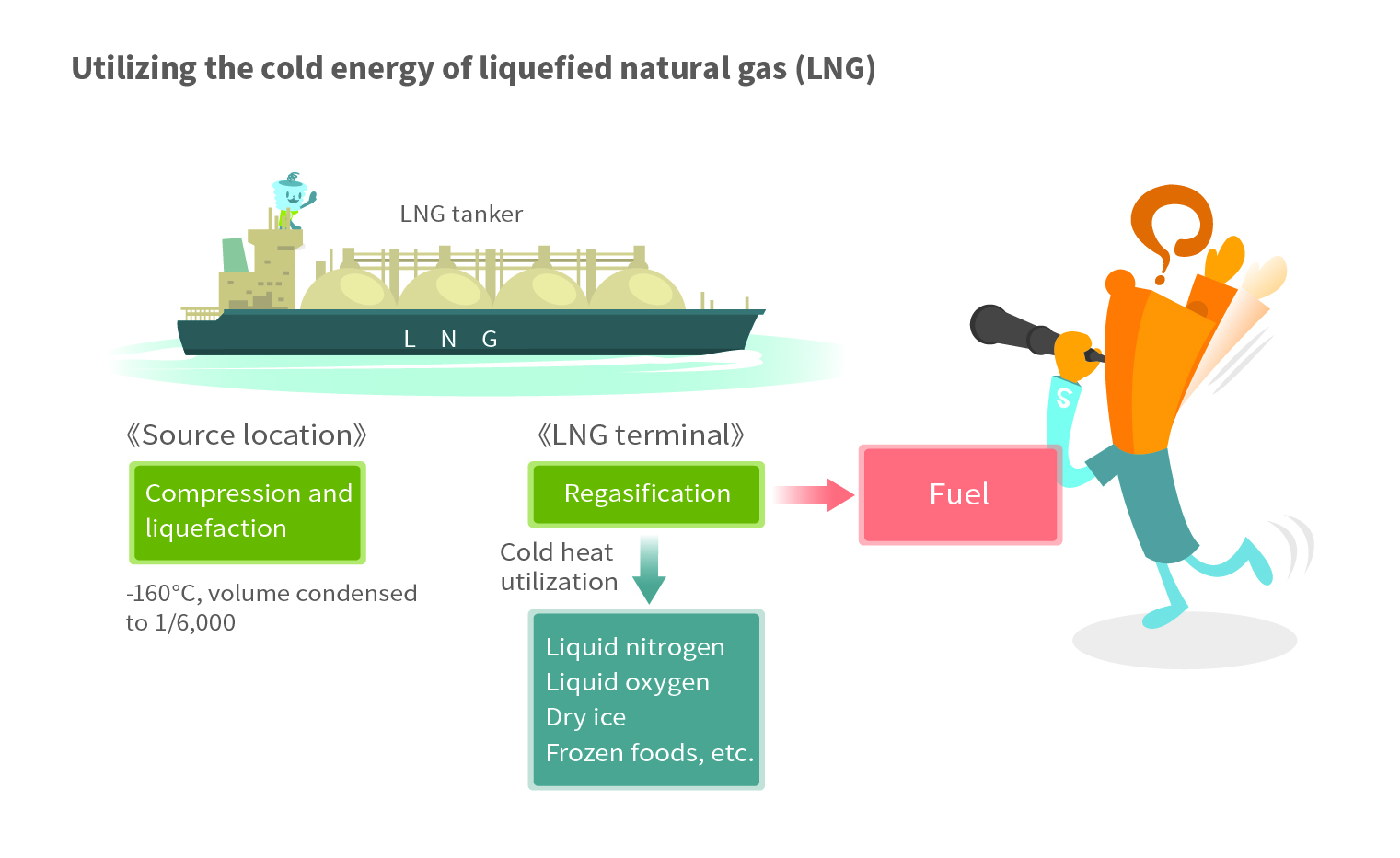
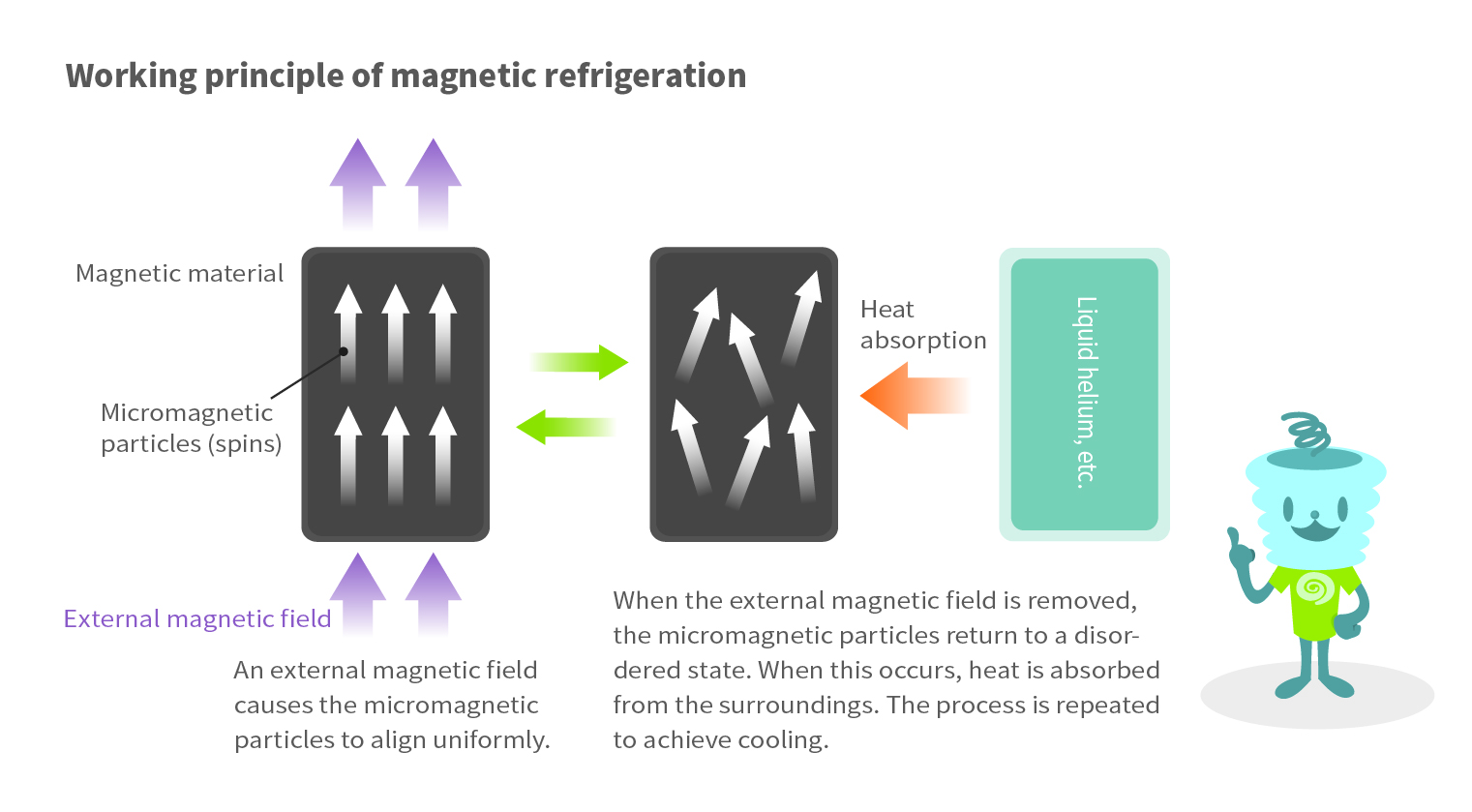
TDK is a comprehensive electronic components manufacturer leading the world in magnetic technology