Knowledge Box
Vol. 2 Robotic cars and sensing technology bring us closer to autonomous driving
People, things, and information linked by networks—this is the age of the cloud. Along with the advancement of ITS (Intelligent Transport Systems) and telematics, automobiles and roads are increasingly networked as well, and the development of autonomous driving systems is progressing at a rapid pitch in various locations around the world. One of the key technologies towards the realization of safe and pleasant autonomous driving is sensing technology that allows precise acquisition of vehicle position and peripheral information.
The robotic car of the near future—a mobile office and mobile living room
The convenience of not having to drive oneself is not the only advantage of a robotic car. The number of people killed in traffic accidents worldwide exceeds one million. About half of these are pedestrians or persons riding a bicycle or motorbike, and a large percentage of accidents are caused by human error. With an autonomous driving system that constantly monitors and scans the situation around the vehicle, failure by the driver to notice something, wrong assumptions, overconfidence in one's driving abilities and other types of human errors can be avoided, which should result in a drastic reduction in the number of traffic accidents.
Advances made in the areas of sensing technology and information processing are of great significance with a view towards making robotic cars a reality. Some automobiles already incorporate ACC (Adaptive Cruise Control) systems that can maintain a proper distance from a preceding car, automatic braking systems for collision avoidance, lane keeping assist systems, and other assistive features that partially approach the realm of autonomous driving.
Robotic cars have currently reached the level where experiments are being carried out on public roads, with practical realization being targeted for the second half of 2020s. The cars of the near future are envisioned to be more like moving offices and moving living rooms. Once autonomous driving is also realized for trucks, the patterns of motorization and goods distribution are bound to undergo a major change.
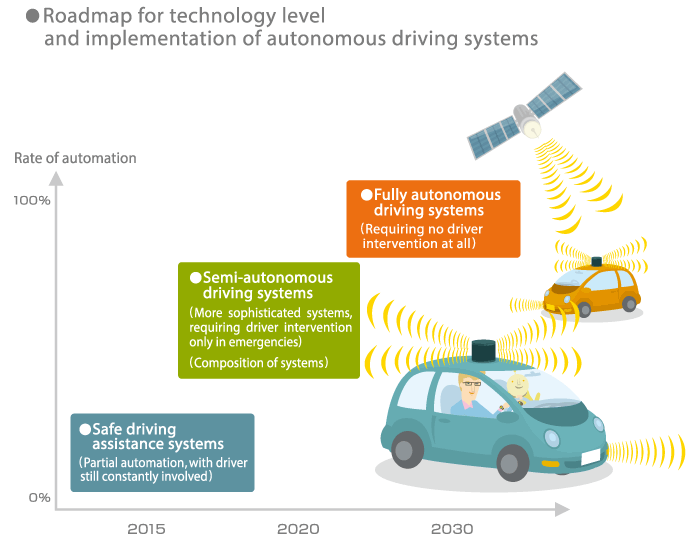
Laser radar to serve as highly capable "eyes" of the robotic car
An automobile comprises a large number of many kinds of sensors, which can be categorized for example as propulsion, body, safety, and info-communication related. Sensors that monitor the vicinity of the vehicle for accident prevention use various technologies such as millimeter wave radar, infrared radar, optical cameras etc. Millimeter wave radar using radio technology can identify objects at fairly large distances and has the advantage of being relatively unaffected by factors such as darkness, precipitation, fog etc. However, low resolution is a drawback of this system. Because resolution is determined by wavelength, systems using infrared radar with a shorter wavelength than radio waves also are in use. These provide better resolution, but their identification range is comparatively short, and they tend to be adversely affected by bad weather conditions. Since each approach has its advantages and disadvantages, monitoring system are adopting a combination of multiple sensors of different types.
For a robotic car capable of autonomous driving, accurate determination of the vehicle's position and of the peripheral situation is absolutely necessary. This means that such a car requires more capable "eyes" than what has been available so far. One possibility is laser radar, also known as LIDAR (Light Detection and Ranging). The principle is the same as a 3D laser scanner used for purposes such as surveying of structures, where a laser beam scans an object to measure the direction and distance of an object. In the case of a robotic car, such a system can be mounted for example on the roof to scan the periphery in a 360 degree arc as well as in the vertical direction. The point cloud data obtained in this way are processed by a computer to create a 3D map of the surroundings in real time, which is compared to GPS based position information, map data etc., thereby enabling autonomous driving.
This has brought the robotic car from a mere dream into the realm of reality, but there are still significant hurdles to be overcome. On public roads, unexpected situations may be encountered suddenly, such as disasters, changing weather conditions, and so on. The development of artificial intelligence (AI) that allows coping with such situations on a flexible case by case basis is therefore still required.

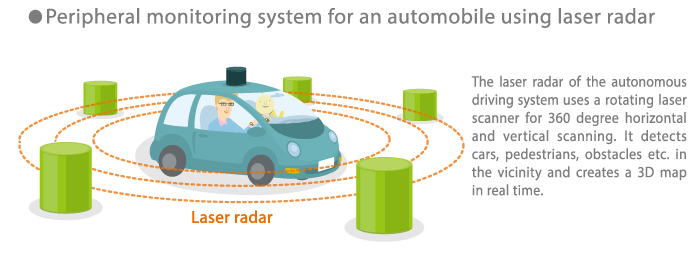
TMR angle sensors from TDK contribute to economic driving
In recent years, sensing technology is also making a major contribution to improved fuel economy in automobiles. The four-cycle engine in a car operates by drawing and compressing a mixture of air and fuel. When the piston reaches the top dead center, the spark from the spark plug ignites the mixture which combusts and expands, thereby pushing the piston downwards. The optimal timing and amount of injected fuel are calculated by the ECU (Engine Control Unit), based on information from a crank angle sensor. However, in multicylinder engines, the crank angle alone is not enough to determine the proper valve open/close timing for each cylinder. Therefore a so-called gear pulser as well as a cam angle sensor are attached to the rotating shaft of the cam that opens and closes the valve, and the signals from these sensors are used as additional information.
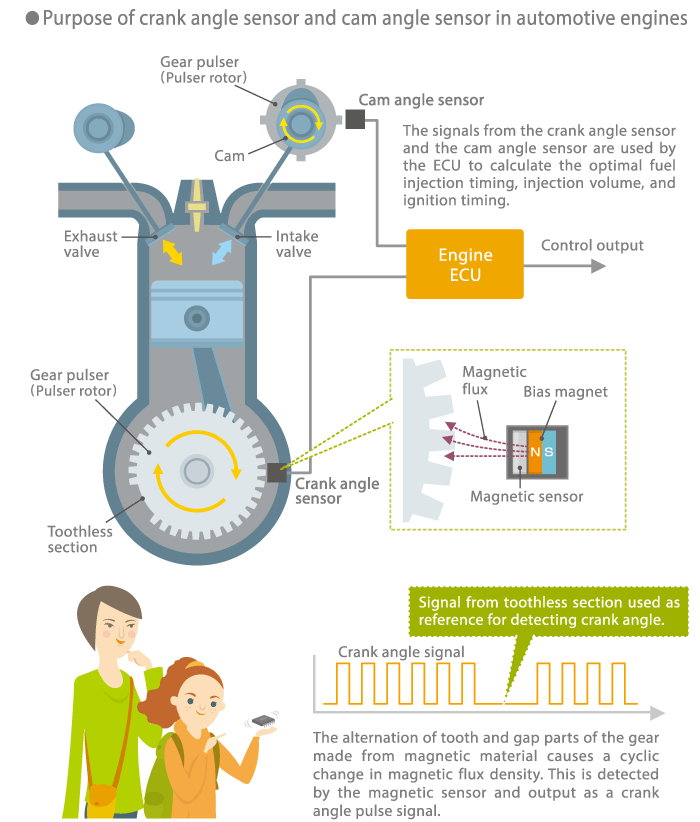
Various principles are in use for crank angle and cam angle sensors. The most common type is the wireless magnetic sensor which is less affected by factors such as wear and dust. A toothed gear pulser (pulser rotor) made of magnetic material is attached to the crankshaft and cam shaft, and a wireless magnetic sensor subject to a magnetic field created by a bias magnet is mounted so that it faces the rotor. When the engine runs and turns the gear pulser, the gear teeth and gaps passing by the sensor periodically alter the flux density from the magnet. This is picked up by the magnetic sensor and output as a pulse signal which allows detection of rotation speed and angle. The above device is therefore also called a gear tooth sensor.
The TMR angle sensor developed by TDK is an application of advanced know-how in thin film technology gained through long involvement in manufacturing HDD heads. Unlike existing types, the TMR sensor is characterized by high sensitivity and high output. As an advanced angle sensor it is therefore suitable not only for crank angle and cam angle detection, but also for use in the drive motors of electric and hybrid electric vehicles, as well as in electric power steering motors and similar.
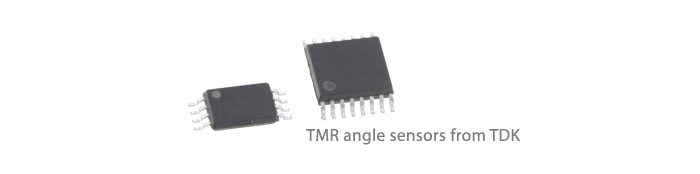
TDK is a comprehensive electronic components manufacturer leading the world in magnetic technology